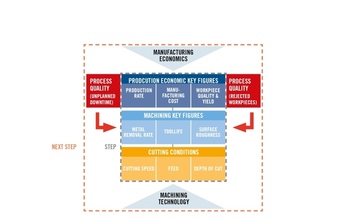
Total image of all elements and how they relate and interact, in a manufacturing plant (NEXT STEP model and concept).
Waste reduction tools
After waste is identified and categorized, a shop should create a plan to reduce or eliminate it. There exists a wide range of tools that enable a manufacturer to pinpoint, quantify, and minimise wasteful practices. For example, analysis of tool usage, manipulation and deterioration will point out trouble areas.
Such analyses have shown that in some cases as much as 20 percent to 30 percent of the tools that personnel defined as worn out were in fact still viable - the remaining tool life was wasted. Establishing clear tool wear criteria and communicating the standards to shop personnel will significantly reduce wasted tool life.
Similarly, machine downtime analyses quantify the time spent in activities such as setup, programming and tool changing. These analyses often indicate that as much as 50 percent to 60 percent of machine downtime is avoidable through a better understanding, execution and coordination of these necessary but time-consuming activities.
The use of interviews, surveys and training programs can uncover a lot of useful information when dealing with personnel issues that lead to waste of intellectual resources as well as unrealized knowledge and skills. As a result, employees perform their jobs better and build capabilities that maximise personnel productivity.
Management of value-adding, value-enabling, and unneeded activities
At the start of the 20th century, American industrial engineer Fredrick Taylor studied workshop operations and proposed that productivity improvement be driven by eliminating any activities in a process that do not add value to the final product. Modern "lean" manufacturing guidelines follow this same line of thinking.
In machining operations, the only true value-adding activity occurs when the tool is actually cutting metal and making chips. Other actions such as part loading and fixturing, termed value-enabling activities, do not directly add value to the manufactured product but are required to allow the value-adding activity to occur.
(Continued on next page)