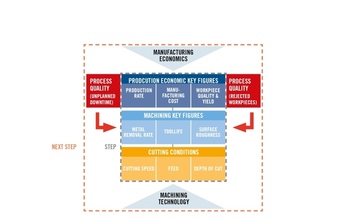
Total image of all elements and how they relate and interact, in a manufacturing plant (NEXT STEP model and concept).
Somewhere there is a combination of cutting conditions that result in a balance of productive output and manufacturing cost. Figure 4 shows the relationship between cutting conditions, productivity and tool and machine costs. (The graph concentrates only on elements that vary as cutting conditions change - material, overhead and administration and engineering costs are not included.) More aggressive conditions are at the right of the axes and higher productivity at the top. The pale blue band at the middle of the graph indicates where cutting conditions produce a balanced blend of productivity (highest output) and economy (lowest cost).
Figure 4 - relationship between cutting conditions, productivy and machining costs. This figure shows a simplified model, not taking into account waste factors.
Accordingly, the third phase of achieving balanced production economics involves determining the optimal combination of cutting conditions for a given situation. It is essential to take into account all the factors in the machining operation to establish a working domain where cutting parameters provide the desired levels of productivity and economy.
The effect of waste on production economics
Unfortunately, the elegant scientific methods of balanced production economics operate at the mercy of waste in the manufacturing system. Waste destroys the balance and occurs in many ways. For example, it is a waste of energy and power when a 60kW machine tool is used in an ongoing application that requires only 15kW. In another situation, when finished workpieces do not meet required levels of quality, the time, money and resources invested in the process are wasted in pursuit of an unacceptable result. Similarly, manufacturing workpieces that needlessly exceed required levels of quality is wasteful, because achieving increased quality increases cost.
A less obvious and less understood occasion of waste is the underuse or misuse of intellectual resources. Certain personnel in a company may possess knowledge or skills that will help the company achieve its goals, but for reasons ranging from poor communication to intra-company politics, the knowledge and skills are not shared and therefore go to waste.
(Continued on next page)