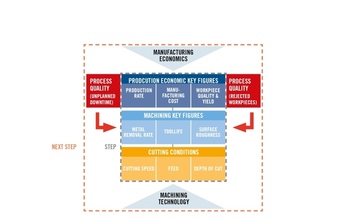
Total image of all elements and how they relate and interact, in a manufacturing plant (NEXT STEP model and concept).
Manufacturers continually seek ways to maximise productivity and efficiency. Today, those efforts frequently involve high-level programs that employ buzzwords that include cloud computing, data-driven manufacturing, cyber-physical systems and Industry4.0. These advanced initiatives are excellent concepts and can produce impressive results. However, manufacturing realities often interfere with the implementation of such ambitious plans, and a critical reality is the presence of uncontrolled waste in the manufacturing process.
Before discussing digitisation and optimisation, it is necessary for a manufacturer to examine its operations, determine where waste occurs, and develop methods to reduce or eliminate it. Controlling waste is the first step in preparing a manufacturing company for the adoption of sophisticated smart manufacturing strategies.
Basics of production economics
Manufacturing consists of a series of transformation processes. A shop forms raw material into finished or semi-finished workpieces through a series of individual transformation operations such as forging, welding or machining. A number of individual elements comprise each operation. The basic elements of machining, for example, include the cutting tool, machine tool, fixtures and coolant supply. Together these elements form a machining system that gets support from related equipment and components in a production system.
Planning, programming and economic management functions surround the production system to form a production environment. The key element of a production environment is people. Although manufacturing today widely utilises computers, robots and other advanced technology, people make the decisions that control the environment overall.
The machining process is based on technical application details regarding tool selection, cutting conditions, programming and workpiece material and fixturing. Other key details include production volume requirements and the specified quality of finished workpieces.
Linking technical application details with economic concerns is called production economics. The goal of the science of production economics is to balance all the factors involved. While technical elements produce desired results in terms of workpiece quality, quantity and timeliness, the operations must be carried out at a cost that enables a business to thrive.
Achieving the balance of output and cost in machining progresses through three phases. The first phase is establishing a reliable machining process. It is essential to minimise unexpected occurrences such as broken tools, uncontrolled chips and resulting destroyed workpieces. A workshop establishes operational reliability by choosing tools with load capacity that meets or exceeds the mechanical, thermal, chemical and tribological loads generated in the machining process.
Figure 2 - Total machinability model developed in STEP
(Continued on next page)