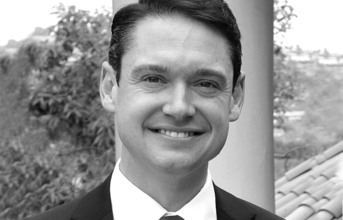
CGTech demonstrated new integration with Kennametal's NOVO application at the 2014 International Machine Tool Show. Tell us more.
Simulation speed is very important to our customers, but so is the amount of time spent preparing a simulation and its accurate representation of the physical process. We continually look for new ways to reduce the time to setup Vericut and ensure it correctly mimics the operations. Online catalogs and tool selectors have become common options for manufacturers looking for the latest tool solutions for their production process.
NOVO goes far beyond the concept of the online catalog by integrating Kennametal's application engineering and production experience. As a result of the CGTech-Kennametal partnership, Vericut users can directly download a Kennametal tool assembly and use it within Vericut software with significantly fewer steps compared to manually configuring a tool for use in a simulation session.
New developments in automated composite fabrication machines are making this technology relevant across sectors. How are you facilitating this evolution?
Productive automated composite lay-up machinery has become a reality, and CGTech has been at the forefront of this evolution. The technology has been driven by aerospace, but is transferring to other industries such as wind, automotive and even shipbuilding. For over 25 years, CGTech has been constantly improving its Vericut suite of software for metal cutting.
But it was in 2004 that CGTech thrust full speed into the world of composites, after being contacted by Boeing (a CGTech customer since 1989) to develop a program for AFP machine simulation for 787 fabrication. This project progressed in 2005 to include the development of a programming solution for AFP machines.
Today, Vericut Composite Applications are used by dozens of companies to program and simulate their automated composite machinery offline, regardless of the make or model of the AFP or ATL machine.
(Continued on the next page)