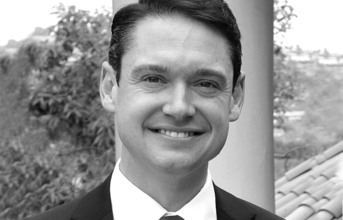
Case study: Reducing prove-out cycle
Generating tool paths for turbine blades can be one of the more complex tasks for NC programmers. With as many as 40,000 lines of code required to mill the blade surfaces to the exact tolerances required, programming and proving-out the data can be a daunting task. Alstom Power Stromerzeugung GmbH recently decided to change its machining strategy for manufacturing turbine blades in order to improve its part accuracy. Alstom switched from multi-spindle to single-spindle machining and invested in five modern Huron machining centres that are networked together and controlled by a Sinumerik-840D.
"The machining process with one spindle is easier than with multiple spindles," explains engineer Rainer Pfeufer. Changing machining strategies also presented an opportunity to improve the NC programming process. Part of that change was looking into a new NC verification solution. Engineers at Alstom use Catia for design. All CAM functionality, measurement, and quality control are handled by internally developed software.
After selecting Vericut for third-party verification, each NC programmer attended two days of basic training where they experienced first-hand the type of results they could expect to achieve. "Depending on the machining task, we can reduce the part programming time by 5 to 10 per cent," says Rainer Pfeufer. Additionally, safety is increased as potential collisions between tool, fixture, workpiece and machine components are recognised in advance. But the real productivity gain was evident on the shopfloor. Because programs are quickly and easily tested on the computer, Alstom was able to dramatically reduce the prove-out cycle.
END