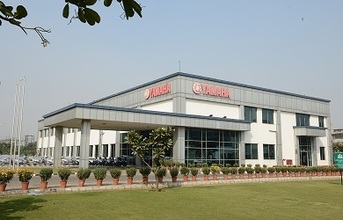
How did the Covid-19 Pandemic affect India Yamaha operations and how did you deal with it?
We all know how the Covid-19 pandemic has caused disruptions globally in the normal routine of everyone whether it is individuals or to the industry or any business. Most important is how quickly and effectively efforts are being taken to install all possible precautionary measures to minimise the impact of spread of infection. As you know, the Indian manufacturing industry is purely dependent on large workforce requirement for parts manufacturing and assembly line operations. So, it is very important as a senior management member on how we respond to these challenges and overcome this situation.
I personally believe an organisation attains the level of excellence by strong management will and leadership by demonstrating proactive preventive measures. Safe workplace for all at Yamaha was the highest priority for us. Being a Japanese MNC, ‘Plan-Do-Check-Action' principle is in our DNA. Covid-19 was not an exception. We focused on the planning part and to do this, a Task Force comprising of members of top management was formed before the lockdown was declared in India. Cross functional groups developed plans and ideas for improvements to deal with the Covid-19 situation.
By the time we received the permission from authorities to resume our operations in both the North & South factory locations, we took a lot of measures in our operations to ensure Covid-Safe workplace. The major challenge for us was to maintain productivity and efficiency of operations as per the standards which were established before this pandemic and at the same time complying 100 percent with the government's Covid-19 Guidelines. We adopted the approach which was - Safety from Home to Home for all our employees. Employees should feel safe right from getting into the company bus and till the time getting off the bus after work.
Our team of engineers used their expertise for re-orientation of layout, process flows, positioning of operatives and other measures for maintaining social distancing norms. Team of volunteers led by medical officer was deputed to offer the required medical assistance to employees at entry gate. Measures have also been taken for touch-free common touch points such as door handles, wash basin taps, drinking water taps etc. We also deployed scientific methods to verify surfaces of common touch points. Through our measures, we ensured that every employee entering the workplace gets a safe and conducive work environment.
Are pre-Covid health and safety manuals obsolete now?
Nothing is Constant - Change is only constant when you intend to excel in the area of occupational health & safety. Be it pre-Covid or Post Covid, Occupational Health & Safety Manuals are dynamic and we keep on reviewing it for the betterment of work environment. At Yamaha, we have extended our thought process of risk assessment from identification of workplace hazard to determining potential biological hazard which may prevail at actual workplace (Gemba).
Accordingly, mitigation measures planning to nullify effects of hazard also got overhauled. We understood that limiting ourselves to confines of identification of unsafe act and conditions may not be enough in post Covid era; it is critical to identify potential causes of infection at actual workplace. If we correctly identify these hazards, we can control potential causes of infections at workplace.
What are some of the major changes that the industry with regards to the working environment and culture?
In my opinion senior management in any organisation must show a strong commitment towards safety for everyone and must adopt the most appropriate approach. We must ensure that all systems are set up to support our commitment. Most importantly, emphasis must be put on education and awareness of employees. In the current scenario, we have entirely changed the way our employees use to work at our workplace earlier. I will just provide few examples of what we have done at Yamaha to ensure safety of our employees.
• Boarding in the employee bus to deboarding from the bus, social distancing is ensured.
• At entry gates, every employee declares his/her health status.
• Every employee goes through mandatory thermal scanning and sanitizes his/her hands.
• While leaving the workplace also, there is mandatory thermal scanning of employees to ensure that all employees are leaving the workplace in healthy condition.
• Frequent sanitization of common areas & touch points.
• Maintaining social distancing during Lunch & Tea breaks by providing partitions at tables.
We have also implemented certain education and awareness methods:
• Announcements through Public Address System.
• Point & Call method to verify PPE adherence before morning exercise.
• Visualization across the plant through Awareness posters.
• Several other training initiatives, Group Activity, Quiz competition - Awareness sessions & Awards by Top Management at shopfloor.
What new set of safety standards and health strategies need to be put in place for future shopfloors to remain functional?
For total employee involvement, we have the concept of My Safety, My Responsibility. We further extended this belief to My Machine, My Responsibility. The idea is to create ‘Ownership Mind' among employees. When employee owns his workplace and machines, he shifts himself from the reactive mode to interdependent mode. In reactive mode, he depends on supervision to follow safety rules and shifts to his natural attitude as soon as he finds out that nobody is watching him. Whereas when employee owns his workplace, he not only ensures safety for himself but also for his colleagues.
At the same time, it is important to make line managers understand the concept in broader way in order to identify and reinforce a risk-free behaviour at shopfloors.
What kind of innovative approaches are you taking at your organisation to improve effectiveness and enhance monitoring capabilities on the shopfloor?
Innovation is one of the core values at Yamaha; I feel innovation does not necessarily mean ‘Eureka Moment'. Small Kaizens that helps to uplift work conditions above the standard improving any of the PQCDSME parameters should be encouraged.
At Yamaha, we have implemented the concept of Small Group Activity (SGA) to create a sense of Ownership and Responsibility among the Employees. Entire employee strength is divided into small groups of 15-20 employees. These small groups are encouraged to implement at least one kaizen to prevent or control COVID 19 infections in each month in their respective work areas. Around 100 nos. of such groups are formed at each plant location of Yamaha.
Has Covid-19 also made us alert enough to plan and prepare for similar large-scale future outbreaks?
Yes definitely, this pandemic has reaffirmed the need for robust Business Continuity Planning. COVID 19 has signalled not only to make preparedness plan but prepare for real time situation and I always suggest that wherever feasible, we must conduct rehearsal of implementation plan. It will instil confidence among members of the response team.
I would also say, not to confine to prepare for emergencies like pandemic but there is an urgent need to take holistic long-term approach while planning for business continuity. Culture of ‘Work from Home' started with this pandemic is going to stay with us longer than the COVID 19 pandemic itself. Methods such as video conferencing and reducing travel carbon foot will also become way of working in corporates.
How can technology be leveraged to educate and train shopfloor employees in the New Normal?
I would say survival in these tough times has been possible only by leveraging technology. Education and training at shopfloor is also not an exception. In the era of new normal, focus has shifted from classroom training. At Yamaha, we have concept of providing learning through prototype machine that gives an environment of workplace away from Gemba. We call this arrangement ‘Safety DOJO', at Safety DOJO employees get practical insight by touch and feeling. Layout in Safety DOJO area is arranged to ensure social distancing. Practical learning in this manner remains with the employees in longer run with periodic refresher sessions.
Similarly at the Yamaha Technical Academy, we have also started remote education and training of our dealership service personnel to ensure skill upgradation of staff and continuity of excellent service to our esteemed customers.
Remote education and training has helped to maintain real time interaction and at the same time ensures physical distancing with emotional connect.
Can manufacturing companies use AI, machine learning and data analytics to predict disruptions and develop training simulations to mitigate risks related to the health and safety of their workforce to increase organisational resilience?
In Indian manufacturing, specifically in the automobile industries, the era of artificial intelligence (AI) is yet to begin. Currently, it is limited to provision of Auto Guided Vehicle (AGV) in assembly line, robotic welding, robotic lifting of metal sheets in press machines. History data and data analytics in CNC, PLC and DCS machines help to understand and analyse operational parameters and disruptions during the working that help engineers to schedule predictive and preventive maintenance. These all measures primarily help to mitigate risks related to the health and safety of the employees besides safeguarding the machineries.
Still, I feel there is a long way to go. The binary language is going to bring a revolution in manufacturing. Not only the health & safety aspect but also the entire business operation is going to get benefitted with AI. AI will become necessary and an integral part of almost any manufacturing process in coming days.
How can the industry develop a unified vision and standards for safety and health of manufacturing professionals?
This is a very valid concern and practical thought. There is an immediate need of mutual collaboration among industries to bring a common vision and standard for safety and health of manufacturing professionals. There are few Government and non-government entities such as National Safety Council, Directorate General of Factory Advice Service & Labour Institute (DGFASLI), SIAM, FICCI, CII, etc. who are working in this direction.
Having a unified vision and standardisation of health & safety practices will not only protect but add value in lives of manufacturing professionals. In my view, all industries can join hands through any of the above-mentioned agencies to develop a common vision and uplift standards of safety & health of employees. When the best and intelligent minds are shared for common cause of the society, overall industrial culture will improve for better.
END