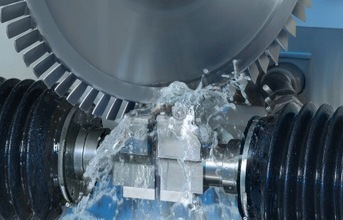
Gentle material removal - fast processes
In view of this, the PECM technology supplied by EMAG ECM based in Germany is currently being studied very closely by many OEMs and their suppliers. The electro-chemical process removes material without contact and causes minimal tool wear while being fast and reliable.
The basic principle is simple to explain: during the process, the workpiece becomes the positive anode and the tool the negative cathode. An electrolyte solution flows between them, removing metal ions from the workpiece. The form of the cathode (tool), with its active, conductive zones results in material removal from the workpiece at the required component contours. Ring ducts, grooves, bell hollows and other contours can be produced without contact, but with very high precision and excellent surface quality.
With their PECM technology, the experts from EMAG ECM have developed this process in a targeted manner and tuned it to perfection. Two factors play a major role in this: firstly, the gap between the workpiece and tool, through which the electrolyte solution flows, is particularly narrow. And secondly, the supply of electrolyte solution is enhanced by a mechanical oscillation motion. Both factors together ensure that that material removal is even more effective and precise.
From single turbine blades to the blisk
EMAG ECM has two machine types for the different machining tasks of engine production: while the small model PO 100 SF is designed for machining single turbine blades, the larger PO 900 BF is for machining the complete, and therefore much larger, blisk. The systems differ in machining area size, footprints, generator capacity and the number of machining axes with precise PECM technology and EMAG high performance components available in both.
"We launched the PO 900 BF in 2011 for blisk machining. The PO 100 SF development was the second stage in 2013 when an ever increasing number of customers demanded an electro-chemical machine solution for single blades. We now have an ideal basis for the development of precise, cost-efficient production solutions for small and large engine components," says Richard Keller, member of the Board of Directors at EMAG ECM GmbH. Both these machines also provide the user with central EMAG innovations such as a Mineralit® polymer concrete machine base, intelligent software and hardware interfaces and efficient automation solutions.
(Continued on the next page)