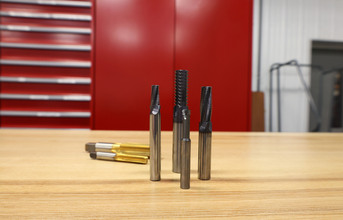
There are many elements to consider when threading a workpiece. When is a solid carbide thread mill better than an indexable? How does the workpiece material behaviour impact thread milling? Understanding your program as well as diagnosing issues that arise are just as important. Luckily, thread milling can be better understood by asking five specific questions.
When Would You Want To Use A Thread Mill Instead Of Tap?
There are many instances where you would want to consider using a thread mill instead of a tap. In numerous cases, this comes back to one common issue: taps break. Because the tap is the same size as the hole, there is a lot of pressure when you are forcing the threads into the hole—even more so in difficult-to-machine materials. Additionally, a tap's cutting edges are constantly in the cut, thus generating more heat. A thread mill on the other hand has little contact with the material, and the heat generated is much lower—an added benefit in any manufacturing process. Finally, when using a tap, chips are more difficult to form and remove.
All the factors above lend themselves to tool failure. When the tap breaks off, it often results in a scrapped part, so using a tap works better when it is an inexpensive part being made. If it is a more expensive part and the tap breaks, you are now faced with the challenge of trying to remove the tap and salvage your part. This is a time-consuming operation that impacts your part's quality and manufacturing cost.
Not only would you want to thread mill whenever the part is expensive, but you would also want to thread mill when working with a large hole diameter. Of course, a tap is just as large as the hole, so for a four inch thread diameter, you need a four inch diameter tap. Instead of buying this expensive, large piece of metal or storing taps for every thread size, you could buy an off-the-shelf thread mill and interpolate the thread into multiple thread sizes including those large diameters. Lastly, thread mills consume significantly less power from your machine in the instance of large diameters.
Other advantages of thread mills include the ability to hold tight tolerances by controlling the tool's cutting path. As the tool shrinks slightly from wear, you can easily compensate for this at the machine by using tool diameter offsets.
Nevertheless, there are occasions where tapping may be the better choice over thread milling. For example, you would want to use a tap when machining long lengths of thread. Due to the lack of radial load, there is no concern about the tap's stability or tool deflection. In addition, when speed is preferred over thread quality, taps are again the better choice. In many applications, a tap will have a shorter cycle time than a thread mill. However, this still comes with the risk of breaking the tap and spending your valuable time to get it removed.
When Should You Use Solid Carbide Thread Mills Vs. Indexable Thread Mills?
In choosing to thread mill, you have the option of solid carbide or indexable thread mills for your application. This choice often comes down to the needs of the application in terms of quality, repeatability and flexibility.
Solid carbide thread mills
Quality and performance are key advantages of solid carbide thread mills. Solid carbide thread mills run and cut faster every time. Having constant surface footage between two different diameters will result in a different RPM. Due to their smaller cutter diameter, solid carbide thread mills will run at a higher RPM. In combination with typically having more flutes, this will result in a faster penetration rate (in/min or mm/min) and improved cycle time. These tools typically outperform indexable thread mills in terms of quality because threads are being ground at the same time. This improves the consistency of threads. With a smaller cutter diameter, there is less contact with the workpiece, resulting in less heat generation and deflection as well.
Indexable thread mills
Most users are attracted to indexable thread mills because they provide the ability to change out thread forms frequently. You can take one body and change out inserts, and the machine is up and running with different forms or pitches rather quickly. Ultimately, this makes indexable thread mills better for low production batches as well as job shop type of work with a lot of change over and variation in the manufacturing. This again comes back to the flexibility of the tooling. You have a one-time purchase of the body and then switch over the inserts as needed.
All in all, a thread mill is simply milling a thread form and a pitch and can usually be used for both left and right-hand threads, internal or external, multiple start threads and various tolerances.
How Does The Material Impact A Thread Milling Application?
Material removal in threading is no different than any other manufacturing process like boring or turning. There are always two things to consider:
• How much material is being removed?
• What is the material like to machine?
The first question can be answered by the thread's pitch. While a fine pitch does not require much material to be removed, a course pitch requires a lot of material to be removed. The combination of these two questions will also help you determine whether your material can be removed in one pass or not. Regardless of how many passes you use to remove the material, just like with boring or turning, a finish pass can be used for improved quality. This is often referred to as a spring pass. If needed, you should refer to the technical section of your manufacturer's catalogue or an available thread mill programming software like InstaCode to choose the number of passes that are right for you.
What Are The Best Practices For Programming?
As mentioned above, a thread mill can create a variety of threads like left or right-hand, internal or external by simply manipulating the program/tool path. Writing a program in incremental movements instead of absolute is always preferred. In doing so, you can insert your code for the threading portion as a sub-program or sub-routine. This is beneficial when threading multiple holes because it provides a single place for program edits. This also allows you to quickly complete a test run above the part to prove the program. In addition to writing this in incremental movements, an arc-on and arc-off movement will improve the quality of the thread and extend the life of the thread mill.
How Should You Diagnose Issues When Thread Milling?
Because thread mills have radial cutting forces, the deflection should always be kept in mind. Factors mentioned previously like how much material you are removing and what the material is like to machine can be battled by adjusting the number of passes to remove the material as well as the combination of speed and feed. Additionally, consider the tool holder you are using. Because of the radial forces and potential deflection, it is necessary to use tool holders such as milling chucks, hydraulic chucks or shrink fits that minimize deflection. Ultimately, these tooling solutions are more rigid and, therefore, improve the quality of the thread you are machining.
It is also necessary to understand if the programmed tool path is based on the centre of the thread mill or the outer diameter of the thread mill. This changes how wear offsets should be applied in the machine.
While you may encounter additional challenges when machining threads, asking these five questions aids in building the foundation for a successful application.
source: Allied Machines