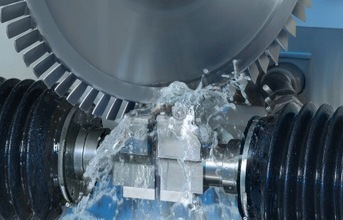
Blisk (bladed disk) volumes in aircraft production are increasing massively. Large engines now have several of these high pressure compressors which are manufactured from a single piece of high performance, often exotic alloy materials.
The efficient machining of these materials is therefore becoming a focal point for project planning with a wide range of potential methods and combinations thereof available, from mechanical cutting to water jet cutting.
A recent study by the Fraunhofer Institute for Production Technology (IPT) and the Laboratory of Machine Tools and Production Engineering (WZL) at RWTH Aachen (Germany) has now shown that Precise Electro-Chemical Machining (PECM) from EMAG drastically cuts costs for users, particularly for dressing the component surface.
Components inside an aircraft engine are exposed to extreme stresses, high temperatures and long service lives. Developers, therefore, use very hard, heat-resistant materials such as nickel-based super alloys for the construction of blisks and disks with single blades.
This development presents a range of problems to manufacturing engineers, since conventional cutting methods become uneconomical as the material hardness increases and the service life of expensive tools drops, therefore causing unit costs to rise.
A recent study by the specialists at Fraunhofer IPT, together with WZL and EMAG ECM GmbH, compared a total of seven different blisk machining strategies, from multi-axis milling, combined with polishing to high pressure water jet cutting combined with PECM dressing.
The results are impressive: for an assumed production volume of 800 nickel-based HPC blisks, the unit costs can be reduced by more than 50 percent compared to mechanical cutting if users adopt the correct machining strategy. PECM dressing proves to be the essential final process to make radical improvements to the efficiency of the production process.
(Continued on the next page)