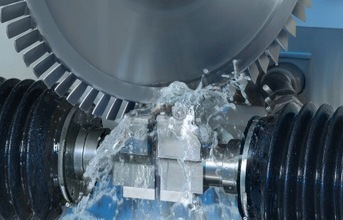
Components certified for practice
This method has already been implemented into actual production with top results. For example, a well-known engine manufacturer has already certified single blades made on the PO 100 SF for use in aircraft in 2014 - unusually quickly after the start of production of the machine at a supplier's plant. A similar stage is currently pending for blisk production.
Components from a whole host of engine companies are currently in the qualification phase for use in practice. "The technology is currently in the validation phase in a number of test programs" states Keller to sum up the current work of EMAG ECM. "The long-term strategic focus on these components and application technology is proving successful and each additional certification of components manufactured with PECM will only boost our sales success."
The geometric machining precision is one of the main factors behind the technology's success. In addition, it produces high surface quality with low peak-to-valley heights. Subsequent finishing processes on the blades, such as slide grinding, are therefore no longer required or can be completed much quicker - both of which result in a further reduction in unit costs. This is a massive plus point for a component which is becoming ever more important and whose volumes are rising massively.
Source: EMAG
END