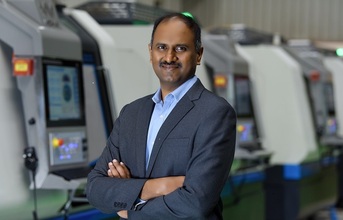
In 1938, metallurgist Philip M. McKenna created a tungsten-titanium carbide alloy for cutting tools that provided a productivity breakthrough in the machining of steel. With his invention, Philip started the McKenna Metals Company in Latrobe, Pennsylvania. Later renamed Kennametal, the corporation has become a world leader in the metalworking industry and is headquartered in Pittsburgh.
Kennametal's journey in India commenced in 1964 when Widia India Private Limited was incorporated in Bengaluru with a strength of 30 employees and one shaping plant. Kennametal acquired Widia in 2003 and established Kennametal India Limited. Today, the company continues to be headquartered in Bengaluru with a modern manufacturing facility and offices in eight territories that serve customers across the length and the breadth of the region.
In a chat with The Machinist team, Vijaykrishnan Venkatesan, Managing Director, Kennametal India Ltd, described the journey of the company.
Take us through your business activities in terms of product portfolios and the sectors to which you cater.
Kennametal is an industrial technology leader in materials science, tooling and wear-resistant solutions for customers across the aerospace, earthworks, energy, general engineering and transportation industries. Our metal cutting segment is dedicated to delivering world-class metalworking solutions and services through our two trusted brands: Kennametal and WIDIA. Through these brands, we offer a complete portfolio of precision-engineered products and custom solution services. With an array of milling, turning, hole-making, threading and tooling systems products, backed by a skilled network of authorised distributor partners and spares support, our customers can find everything they need from one single source.
Our machining solutions group manufactures special purpose machines, tool and cutter grinding machines, as well as fixture and tooling solutions through the WIDMA brand. Several customers are benefiting from the expertise of WIDMA in engineering the most complex components with precision, right from microtools to large structural parts for railways and aerospace.
Our infrastructure segment is a global market leader in wear solutions, engineered components, earth cutting and construction tools that deliver productivity, reliability and extended life to a wide range of industries in the harshest environment. We offer expertise in matching our advanced material solutions and technologies to various applications. This helps customers solve their biggest wear problems, avoid costly downtime, prevent catastrophic failures and achieve significant savings.
What are the end-to-end additive manufacturing solutions provided by Kennametal and how relevant are they in the Indian market today?
Leveraging our long-standing expertise in materials and manufacturing, Kennametal offers end-to-end Additive Manufacturing (AM) solutions, from metal powder feedstock, to design optimisation and rapid prototyping, to post-print processing and fully finished components.
While AM has existed for a long time, we are witnessing its traction in recent years as a significant lever to drive the Industry 4.0 revolution, with the potential to transform conventional production processes. As the name suggests, AM implies adding material in layers to create a finished product.
Additive manufacturing offers opportunities to produce complex geometries that would be impossible using traditional manufacturing methods, shorten development cycles and lead times, consolidate parts and improve performance through materials and design. India is currently at a nascent stage of technology adoption with a largely unexplored market for AM that is estimated to grow significantly in the coming years.
What was the rationale behind setting up Rapid Response Centres? How it is serving a customer-centric approach to your business activities?
Kennametal Rapid Response Centres offer reconditioning services and localised production of simple and special round tool drills and end mills. Tools are reconditioned to Kennametal original coatings and geometries for like-new performance and reliability. With repeated reconditioning, tooling costs can be reduced by 50 per cent or more in many cases, compared to the cost of purchasing new tools.
In India, we have reconditioning centres at five locations with easy access to customers and a quick turnaround time. These centres offer a win-win solution, as they enable our customers to quickly access Kennametal quality and precision at a lower cost, while our brand can acquire a higher market share in the value segment.
How important Is sustainability to your company's mission and vision and how are you contributing towards it?
At Kennametal, sustainability is an integral part of doing business with a consciousness towards the ecosystem in which we operate. We are committed to programs that ensure: the health and safety of our employees; a diverse, engaged, and ethical workforce; the development and enrichment of the communities where our employees live and work; and protection of the environment for future generations. Last year, Kennametal released its Environmental, Social and Governance (ESG) report that provides a comprehensive summary of the progress and opportunities in this area. Some highlights of our global ESG during 2020 include:
- Implementing extensive safety protocols to protect the health and safety of our employees while continuing to serve customers during the COVID-19 pandemic
- Proactively eliminating or mitigating more than 690 potential injury risks and
- Reinforcing our commitment to a culture of accountability to employees, customers, shareholders, the environment and the communities in which we operate.
Our Bengaluru manufacturing facility, for example, has adopted various measures to ensure minimum impact on the environment. For instance, close to 80 per cent of our energy comes from solar, we ensure optimum water and waste recycling to reduce freshwater consumption significantly and our emissions are well within the stipulated PCB (Pollution Control Board) norms.
Take us through your CSR initiatives.
Our corporate social responsibility platform is built on a three-pronged framework: environmental, social and governance. Through credible NGO partners, we are involved in various projects to make a meaningful impact around our manufacturing facility. In one of the key initiatives, we have partnered with the NGO, India Literacy Project, to support seven government schools for underprivileged children in creating a multi-dimensional learning space by funding ‘smart' classrooms. From computer and science labs to libraries, the project is giving nearly 2,500 local students access to the critical educational infrastructure needed to build skills for the future. Through the NGO Katalyst, Kennametal India is sponsoring deserving girl students pursuing engineering courses, enabling them to gain a level playing field in their professional careers, while propelling gender equity.
How is innovation and R&D contributing to the company's overall business strategy?
Core to who we are as a company, our innovation helps solve our customers' biggest challenges so they can deliver the products and services we rely on every day. We have a R&D and engineering base in Bengaluru that works closely with the global organisation to continuously develop and commercialise both new and improved offerings suited for the Indian market. This DSIR (Department of Scientific and Industrial Research) recognised R&D centre is equipped with advanced labs and testing equipment managed by a team of engineering and technical experts.
Kennametal has recently launched the VXF™ series of high-feed cutters that combine the best features of round and square inserts to boost metal removal rates, achieve the next level of high-feed milling, and make it the first choice for deep cavities. VXF high-feed mills master demanding workpiece shapes in up to 9 different machining operations and 5 material types, making it a versatile solution for various industries. Another newly launched cutter, VSM890, delivers superior metal removal rates through high-performance grades and chip breakers. It is applicable for a wide range of workpiece materials: aluminium, steel, cast iron, titanium, stainless steel and high-temp alloys- and addresses light machining to heavy-roughing jobs. We also launched TOP DRILL™ Modular X (TDMX) for high-demanding drilling applications and Varimill Xtreme for aggressive machining conditions from the WIDIA brand as our recent launches.
Take us through the company's manufacturing facilities and capacity utilisation.
We have a state-of-the-art manufacturing facility in Bengaluru, spread over a campus of 29 acres. Our manufacturing setup is divided into 8 production units that develop products, both for the domestic and international markets. It complies with necessary environmental norms as mentioned earlier. Kennametal has made a significant investment to modernise its facilities globally, and as part of that initiative, we are deploying advanced technology and equipment here in Bengaluru that will bring value to our customers through improved quality, product performance, innovation and delivery.