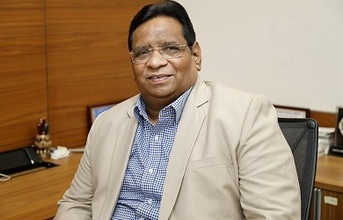
"A key step in risk mitigation against future disruptions will be the creation of flexible operating models, increasing automation and reliance on technology to minimise human interface," says Rajendra Chunodkar, President – Manufacturing Operations, Lupin Limited,
Has Covid-19 put you through the toughest leadership test of all times?
A humanitarian crisis of the scale of the COVID-19 pandemic has ushered in a period of great uncertainty and change. While industries and individuals are grappling with the challenges, the global pharmaceutical industry has taken center stage in the fight against COVID-19.
Our contribution during this critical time ranges from vaccine development, research on repurposed and novel medicines, while ensuring supply of essential drugs amidst unprecedented disruption. The industry is also supporting the frontline workers and the needy, all while safeguarding the health and safety of our employees. Despite the multiple headwinds, the pharma industry has risen to meet the challenges head on.
To do all this and be prepared for more, all leaders have had to call upon great reserves of strength, previous learnings and the ability to think out of the box so that daily challenges can be met and new ones anticipated.
How has the Covid-19 pandemic impacted Lupin's operations?Being a part of Essential Services, the pharma industry was particularly responsive to the disruption caused by COVID-19 and took exemplary and expedited steps to ensure business continuity. At Lupin, we outlined two main priorities, to keep our employees safe and to maintain our supply of life-saving medicines for the patients and communities in need.
Our manufacturing leaders stepped up to ensure that while we continued manufacturing our much-needed essential medicines, the safety of our people was not compromised.
Our manufacturing and supply chain teams responded with characteristic agility to ensure supply continuity while we rapidly adapted to new ways of working for our manufacturing, research, field and office staff. Right from screening and ensuring social distancing at work or in cafeterias, to using Personal Protective Equipment (PPE) at all times, we left no stone unturned. Our supply chain and procurement teams also ensured optimal supply of PPE and sanitisation materials, while there was an ongoing global shortage.
To overcome any input material disruptions and logistic challenges, our commercial and operational teams worked closely with our customers and government agencies to ensure that we are able to maintain a consistent supply of our products, including those being used for the treatment of COVID-19. The Government of India had announced several incentives earlier for setting up API units domestically to boost manufacturing within India and mitigate risk of supply chain shocks from external sources. We used this opportunity to reassess our manufacturing footprint, de-risk in-line products and engrain flawless execution as a key differentiator. The rapid execution and speed of socialising these best practices globally, demonstrated our agility and spirit of excellence.
What are some of the pre-covid measure implemented at Lupin operations that have enabled efficient operations despite the impact of the pandemic?
Pharma manufacturing in general requires special precautions, a clean environment and other measures such as donning head gear, a mask, full body garments, i.e., changing into uniform while on premises, hand sanitisation, an efficiently designed air handling system which avoids carrying microorganisms during the operations, etc. So, when COVID specific preventive measures such as masks, protective garments, frequent sanitisation, social distancing, etc. were required to be introduced, majority were already in place at Lupin.
For efficient supply chain management in pharma, redundancy or back up is very important for raw materials and packing material supply as well as an alternate approved manufacturing site for the same product. This helped Lupin to maintain continuous supply of medicines to patients in need, whenever there was an issue with a certain supplier or any of our manufacturing sites.
Lupin also always maintains a healthy inventory level of raw materials, APIs and finished products, which greatly helped during the early stages of the Lockdown when we experienced disruption in logistics.
Considering the contingency plans implemented during the pandemic to ensure efficient operations, how can manufacturing leaders leverage on these learnings for the future?
The COVID-19 pandemic was an unforeseen event for most and put lot of stress and strain on operations and personnel to proceed with operations in a safe manner. No pandemic has caused so much disruption compared to COVID-19. But as we have formulated and have new procedures and protocols in place now for such pandemics, we are better prepared for similar disruptions in the future.
Can manufacturing companies use AI, machine learning and data analytics to predict disruptions and develop training simulations to mitigate risks related to the health and safety of their workforce to increase organisational resilience?
A key step in risk mitigation against future disruptions will be the creation of flexible operating models, increasing automation and reliance on technology to minimise human interface.
The increasing need for social distancing and contactless operations has prompted several innovations in processes and operational procedures, entailing investments in new equipment and software and data analytics where required. For example, a simple camera with thermal sensors and facial recognition AI software can instantly detect people with fever. These are being used at our factories now. Another technology uses BLE (Bluetooth Low Energy) beacons such as worker badges, or their smartphones. Using inputs from these, AI can determine the distance between co-workers in real time and if the threshold is exceeded, a warning signal is sent.
Manufacturers want to be able to keep producing and selling during an unstable period. To be able to continue, they will need to adapt quickly to inculcating AI and automation in their processes.
It is important that for contactless operations, paper documentation / approvals are avoided and we are in the process implementation of eDMS, eLog books, eBPR, LIMS, QAMS across our network. Also implementation of automation and robotics are being accelerated across all our manufacturing locations. This will help us not only for contactless operations, but for efficient and cost effective operations.
Many departments at organisations can work from home. The interest in AI here arises not only to substitute humans, but to support them in their daily work. Similarly, high-performing robots can work faster for longer periods at plants. Hence, we see that Industry 4.0 adoption would unleash cost optimisation possibilities and drive efficiencies in ways never imagined before.
What are some of the major changes that the industry needs to bring with regards to the working environment and culture in the New Normal?
Being a part of essential services, the pharma industry has been particularly responsive to the disruption caused by COVID-19 and taken exemplary and expedited steps to ensure business continuity. In fact, the operations model of pharma companies even became a ready working model for resumption of manufacturing operations across industries.
However, in light of the pandemic the industry will also witness massive shifts in R&D, supply chain, operations, digital adoption and talent management. Companies will also have to balance the twin imperatives of maintaining limited headcount and ensuring 100 percent productivity at sites.
At Lupin, we are using this challenge as an opportunity to become more resilient, by upskilling of talent and equipping our people with abilities to work remotely, with a deeper understanding of digital possibilities enabling us to be more efficient and more focused on introducing quality, affordable treatments to market faster to help improve outcomes for patients.
We expect pharma digitisation to result in positive outcomes for research, manufacturing, quality, commercial and other allied operations. An increase in digital promotional activity is also expected with physicians advocating for more patient engagement on virtual platforms and marketing promotions moving onto the virtual space.
However, the industry must also ensure compliance with regulations when dealing with sensitive information. Employees too need to inculcate a safety-first mindset and be receptive to changes in working patterns and privacy norms with requests for recent health and travel information becoming common.
Lupin's Tarapur and Goa sites have implemented centralised Data Acquisition System for real time data capture in manufacturing operations to reduce human errors. Tell us something about the effectiveness of the same.
Our Centralised Data Acquisition System (CDAS) captures all the data generated from various machines, instruments and equipment at a centralised place. The process of manually recording data can now be completely avoided after the implementation of the CDAS at these two sites. These also prevent the transcription errors.
The more important aspect of CDAS is that it is a stepping stone for Data Analytics. We have a plan to use the data analytics for optimising the set process parameters to improve cost efficiency and minimise our ‘Out of Specification' batches. Also, the data generated can be used in predictive maintenance to improve the availability of equipment thus increasing the capacity of the plant.
Since Lupin has manufacturing operations at different geographical locations, what have you done to bring operational harmony in the New Normal?
Lupin has corporate policies and procedures for manufacturing operations, quality systems, infotech, environment, health and safety. In the new normal, the amended procedures are followed at all our manufacturing locations. For any new amendments in the policies, we have training sessions as well.
There is an increasing awareness towards adoption of renewable energy sources by manufacturing plants. What is Lupin doing in this regard?
As a leading pharmaceutical player supplying medicines to over 100 countries across the globe, our sites are certified by all relevant regulatory bodies. Through our environment, health and safety measures we ensure that our procedures and practices in manufacturing our products meet the highest international benchmarks. We continue to upgrade and invest in infrastructure to create a greener footprint of our operations whilst investing in our employees' health and safety through training, process overhauls and technology deployment.
In FY20, our consumption of energy from both renewable and non-renewable sources was 2,981,239 GJ. Of the total energy used in our manufacturing plants and R&D center, 10.3 percent comes from renewable sources. We have also started switching over from furnace oil to cleaner fuel for several of our facilities. To further reduce dependency on fossil fuels, we have installed solar power panels at almost all our facilities.
We have also taken steps to significantly reduce our energy consumption. 2,175 GJ energy was saved by replacing conventional sodium vapour and fluorescent lights by LED lights at five of our API sites. We have installed of motion sensors in offices and warehouses to optimise energy utilisation. We have also introduced plate heat exchangers for hot water generation, installed capacitor banks and heat pumps.
It has been often said that India has the potential to become the ‘pharmacy of the world' in terms of manufacturing prowess. What needs to be done to achieve this vision - both from the industry perspective as well as from the government point of view?
The Indian pharma industry has been playing a significant role in driving better health outcomes across the world through high-quality and affordable generics for years now. Currently, India is the world's largest provider of generic medicines accounting for 20 percent of global generic drug exports in terms of volumes and also has the second-largest number of US Food and Drug Administration (FDA) approvals. India supplies over 60 percent of the global demand for ARV drugs and various vaccines.
Native pharma firms have been quick in capitalising on export opportunities across markets. The pharma exports from India, which include bulk drugs, intermediates, drug formulations, biologicals, Ayush and herbal products and surgicals stood at US$ 16.28 billion in FY20.
However, for long-term value creation, the industry must turn towards complex generics, specialty products and biosimilars. Both complex generics and vaccines present an opportunity to increase the value share of innovative drugs from three percent to 10 percent primarily via exports. The industry has an ambitious vision of achieving industry revenue goal of US$ 120-130 billion by 2030 from the current US$ 43 billion. Pharmaceutical exports should quickly evolve into a key pillar of India's overall trade expansion and diversification strategy.
Some key government interventions such instituting measures to ensure that Indian drugs remain export competitive, with suitable policies to help offset costs, should be prioritised, The government should also consider introducing concessions to help lessen production costs for Indian companies. There should be an increased engagement by Indian Missions abroad to be able to leverage full potential of the pharma industry in newer destinations. Lastly, there is a need to enhance engagement with governments of major export markets to lower regulatory barriers.
END