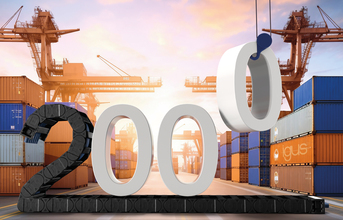
Seaports are under pressure worldwide: to remain competitive, terminals must handle larger ships in shorter periods. Consequently, more and more operators are adopting modern components such as igus's robust energy chains, which are compatible with Industry 4.0. The motion plastics specialist has now equipped its 2,000th ship-to-shore (STS) crane with e-chains, making increasing numbers of terminals future-ready.
According to a recent report by the United Nations Conference on Trade and Development (UNCTAD), over 80 per cent of cross-border trade in goods is now transported by sea. The sector is forecast to grow by an average of 2.4 per cent per year until 2029. This growth is placing pressure on many ports to modernise infrastructure and process larger volumes more rapidly. Technical constraints persist, however—not just due to major structures such as harbour basins, but also due to thousands of smaller components often overlooked. One such example is the traditional festoon system: looped cables that supply the trolley with energy and data.
"To keep up with the increasing speeds and extended travel distances of STS cranes serving ever-larger ships, manufacturers would need to begin motorising the festoons. However, this is complex and prone to faults. There is always the risk of the trolley and festoons falling out of synchronisation, leading to excessive tensile loads, cable damage, and system failures—particularly over long distances," explains Jens Göbel, Industry Manager for Cranes & Material Handling at igus.
"That's why more and more port operators are replacing festoons with energy chain systems." As a result, igus has now equipped its 2,000th STS crane with e-chains.
Tech Up, Cost Down: Switching Systems Offers Many Advantages
This development marks a significant step in the global modernisation of seaports. igus's e-chains offer several advantages over traditional festoons. The igus rol e-chains are made from high-performance plastic, specifically engineered for the industry to ensure long service life and reliable operation under all weather conditions. These systems can operate at speeds of up to 10 m/s without requiring complex motorisation.
Thanks to integrated rollers and a low co-efficient of friction, payloads and acceleration can be increased while maintaining the same push/pull force. Compared with gliding systems, drive energy can be reduced by around 57 per cent—a major benefit amid rising energy costs. The internal separation of the chain is also easily modified, allowing new cables to be inserted with minimal effort—an important advantage in today's fast-paced technological environment.
Popular models such as the heavy-duty roller energy chain P4HD.56.R offer a running performance of over 200,000 km—translating to a service life of up to 15 years. A special clevis-and-tongue design ensures maximum stability under high additional loads, while a pin-and-bore connection made from tribologically optimised plastic helps reduce wear.
Furthermore, all rol e-chains can be fitted with i.Sense sensors for real-time monitoring and predictive maintenance. This reduces maintenance frequency, extends the crane's operational life, and improves overall efficiency. Customers also benefit from a unique four-year guarantee, offering added peace of mind.
Expanding Market Presence
igus's energy chains have gained popularity in Asian ports, known for early adoption of new technologies. Since the development of its first roller energy chains more than 25 years ago—and their initial installation at Shanghai Zhenhua Heavy Industries (ZPMC) in 2000—igus has achieved a market share of around 60% in the new crane segment.
Ports and terminal operators worldwide, including APMT, DP World, and AGL, have followed suit. In 2017, igus celebrated the installation of its 1,000th energy chain in an automated port at APM Terminals Rotterdam. With its 2,000th installation now completed, igus has reached another milestone, reinforcing the critical role of innovation in port logistics.
The company also offers other award-winning solutions such as the igus Mobile Shore Power Outlet (iMSPO)—a flexible shore power connection system that can be moved along the berth depending on a ship's location, including at the Port of Hamburg. Simultaneously, igus has developed maintenance-free high-load bearings that are increasingly used in port cranes. These fibre-reinforced plain bearings not only reduce maintenance costs but also eliminate the risks associated with improper lubrication.
Jens Göbel concludes: "We are confident these technological advances will enable even stronger collaboration with STS crane manufacturers and terminal operators as we continue designing ports that support efficient and sustainable maritime transport for the future."