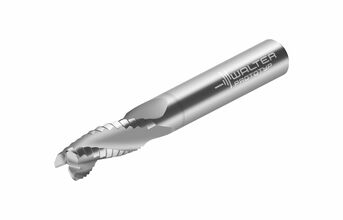
According to a study by the International Aluminium Institute (IAI), global aluminium demand is projected to grow by 40 per cent by 2030, rising from 86.2 million tonnes in 2020 to 119.5 million tonnes. A key sector driving this growth is transportation – spanning bicycles, cars, trucks, and even aircraft. Addressing this dynamic and expanding market, machining specialists such as Walter, based in Tübingen, Germany, have developed a dedicated range of high-performance tools.
High-performance machining systems face new challenges
Aluminium alloys are particularly favoured in applications where high component toughness must be balanced with low weight. This has led to a surge in lightweight construction, particularly within the mobility sector. However, this combination of material properties also presents machining challenges. For example, the high ductility of wrought aluminium alloys can lead to build-up on the cutting edge, and long chips can compromise process reliability. In the aerospace sector, components are often milled from solid billets, with machining volumes reaching up to 95 per cent of the original blank. These parts are also frequently large and complex, making secure clamping more difficult.
To meet these demands, aluminium machining often employs large, cost-intensive machines or machining centres with highly powerful spindles. These are necessary to achieve the required metal removal rates economically. Today, spindle outputs above 80 kW are common, with the latest machine generations delivering around 130 kW.
However, power alone does not make a machining process efficient. The cutting tool plays a crucial role in transferring the machine's theoretical performance to the workpiece. Only with a well-optimised tool and process setup can the full potential of a modern high-performance system be realised both economically and reliably.
Walter has supported customers in meeting these efficiency demands for years with a carefully developed range of tools for aluminium machining. In recent years, the company has significantly expanded its aluminium portfolio. The MD265 Supreme and MC268 Advance solid carbide milling cutters, launched in October 2022, are specifically designed for high-volume machining of ISO N materials such as aluminium alloys.
Innovative micro-geometry boosts process reliability
In developing these new milling cutters, Walter placed particular emphasis on optimising the micro-geometry of the cutting edges. Both feature a unique "V-shaped centre cutting edge with two clearance angles" – a Walter innovation currently unmatched on the market. This geometry allows for angled plunge-cutting into the workpiece with low heat generation and excellent process reliability.
This is a key advantage, particularly at high machining rates, where localised temperatures can reach up to 480 °C under minimum quantity lubrication (MQL). Such temperatures risk altering the material's structure and electrical conductivity, potentially leading to rejection during quality control. Thanks to the new geometry, temperatures remain below 140 °C, preserving the integrity of the material.
Additionally, the cutting edges, Kordel or RAPAX profiles, and flutes are finely polished to minimise material adhesion. This optimised micro-geometry results in smoother cutting and significantly enhanced process reliability. It also allows for reduced cutting forces, thereby lowering spindle load and maximising energy efficiency.
The MC268 Advance, with its Kordel profile, is designed as a versatile roughing tool. Meanwhile, the MD265 Supreme, featuring the RAPAX profile, is tailored for maximum metal removal rates. In 24/7 operations on Al7075 components, the MD265 Supreme achieves removal rates of up to 9.2 litres per minute. This is achieved with a 25 mm diameter cutter, operating at 33,000 rpm, with a 0.15 mm feed per tooth, and cutting depth and width both at 25 mm. The required spindle output is approximately 120 kW, fully utilising the capabilities of the latest machine tools.
Walter DC166 drill delivers 30 per cent productivity gain in aluminium
Since April 2023, Walter's DC166 Supreme solid carbide drills have been available for manufacturers requiring high-speed drilling in aluminium alloys. These drills offer productivity improvements of up to 30 per cent. With enhanced central cooling, a thinner web, and polished flutes, significantly higher feed rates are possible. In some applications, this translates to a 50 per cent reduction in machining time. Additionally, the tool life is extended due to reduced built-up edge formation.
This standard drill, equipped with through-coolant capability, is optimised for use with minimum quantity lubrication (MQL) and emulsion cooling, making it ideal for high-volume aluminium machining.