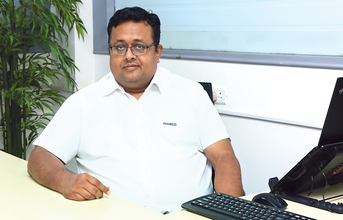
In any organisation, workforce management plays a vital role. What is your take on it?
WABCO India has a very strong Total Employee Involvement (TEI) culture that has been carefully nurtured over three decades and which forms an integral part of our workforce management strategy. Our TEI vehicles like Employee suggestions, Quality Control Circles (QCC), Supervisory Improvement Teams (SIT), Cross Functional Teams (CFT) and task forces, helps in process improvements across functions through enhanced employee collaboration. The TEI culture helps to promote creative thinking among employees, which results in material, labour and capital productivity. For example, capital productivity is improved through better utilisation of machine capacity and upgrading old machines to industry 4.0 standards. Similarly, material productivity is enhanced through Value Analysis, Value Engineering (VAVE) and alternate sourcing practices.
Skills Development is one of the major challenges that the manufacturing industry currently is facing. What are your thoughts on the same?
It is the responsibility of any industry to upgrade their workforce to bridge the gap between meeting customer requirements and their employees' existing skill sets. To develop a competent workforce, we impart need based trainings to the operators, with emphasis on quality for multi skills and involve all employees for the improvements through suggestions scheme and QCC projects. Structured training on specialization & analytical skills is regularly conducted and Total Productive Maintenance (TPM) is leveraged as an effective tool to improve overall productivity. TPM helps to avoid wastage in a quickly changing environment, reduce manufacturing cost, produce a low batch quantity within the shortest possible time & ensures that products sent to customers meet required quality standards. We use Quick Response Six Sigma (QR6S), QC story & Six Sigma DMAIC (Define, Measure, Analyze, Improve, Control) approaches as tools to help improve the problem solving skills of our employees.
(Continued on next page)