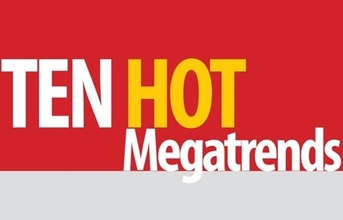
Trend 4
Cluster Manufacturing
Cluster manufacturing relates to the regional concentration of interrelated companies operating along an entire value chain, including manufacturers, service providers, suppliers, key customers, research institutes, universities and trade associations.
These business clusters are often established in a particular geography to network and benefit from physical proximity, core competencies, skilled workforce and specialists, activity base, specialized (physical, and knowledge) infrastructure, and industrial organisation.
The geographic concentration of a cluster provides a unique environment for accelerating technological innovation, stimulating new start-up firms and attracting investments. The critical mass effect often attracts further companies, investors, services and suppliers, as well as creating a pool of skilled labour and increasing innovation through the exchange of ideas.
"When business partners are located close to each other, it becomes easier for companies to exchange information, communicate and share input and/or output and to achieve a mutual benefit (joint development, alliances, joint ventures, etc.). The more links and networks spanned between companies, the more innovative and effective they become." - Thomas Hillek, Partner, Consulting - Strategy & Operations
-----------
Trend 5
Energy/Resource Efficiency
Manufacturing firms across the globe rely on the efficiency of their manufacturing processes to remain competitive in the market. Companies are actively researching, testing and implementing new energy sources, materials, processing technologies and logistics strategies to become more energy efficient and also reduce their carbon footprint and cost of materials.
Manufacturers constantly seeking ways to counteract effects from the rising demand and the drastically increasing competition for energy and raw materials. With continuous incremental improvements and extensive investments, companies are also reducing their environmental impact to meet legal requirements.
The introduction of energy saving technologies and processes and the optimized relationship between resource input and product output should enable efficiency and sustainability at every stage of a product's lifecycle, from production to operation to recycling.
"Commodity prices, energy usage and logistics management are already important for manufacturers to maintain their competitiveness today. However, these factors will become even more crucial in the future given the challenges of the energy market all over the globe and uncertainties about the energy supply as well as customer expectations associated with it." - Dr. Götz Wehberg, Partner, Consulting - Strategy & Operations
-----------
Trend 6
Talent Challenge
The global manufacturing landscape continues to evolve, driven by factors like globalisation, technological advancements and demographic shifts. These factors are in turn driving the demand for higher skills in the manufacturing sector.
Both mature and emerging economies are facing talent shortages. In mature markets, despite the high unemployment rate, companies are struggling to fill manufacturing jobs with the right talent.
Whereas, in the emerging markets, availability of a skilled talent pool is low. Know-how is a competitive advantage and innovation is a growth driver. The lack of a highly skilled, flexible workforce is impacting on the competiveness of manufacturing firms and preventing them from delivering innovation.
"Attracting and retaining appropriately qualified and motivated staff remains a top-of-mind issue for manufacturing companies. Many fear that labour shortages will retard long-term business growth." - Dr. Michael Geke, Partner, Consulting - Strategy & Operations
-----------
Trend 7
Nanotechnology/Nanomanufacturing
Nanotechnology is defined as the combination of material science and technology for manipulating the structure of matter at the molecular level. Nanomanufacturing is the production of materials and manufacturing of parts either from the "bottom up" from nano-scaled materials or "top down" in nano steps for high precision.
Both nanotechnology and nanomanufacturing are providing new capabilities and products to industries like automotive, aerospace, electronics, power, chemical, biomedical and health. Advancements in nanomanufacturing are helping to create new markets for nanoparticles, nanostructures and nanodevices.
Scientists and engineers will develop materials at the nanoscale to take advantage of their enhanced properties such as lighter weight, higher strength, increased control of light spectrum and greater chemical reactivity than their largerscale counterparts. A key understanding of nanotechnology is that it offers not just better products, but a vastly improved manufacturing process.
"Nanotechnology presents the research-based industries with significant challenges and opportunities in risk management. Central to these are the relatively unknown environmental, health and safety exposures arising from nanomaterials through their lifecycle." - Andreas Bartels, Director, Transactions & Restructuring
(Continued on the next page)