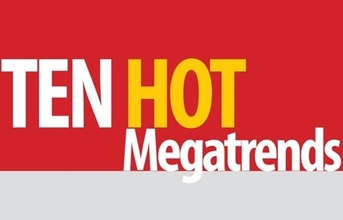
As a consequence of the recent economic turbulence, manufacturers have been forced to increasingly review their financial management processes - especially focusing on risk management and the financial exposure during crisis situations.
This should, however, not lead to companies disregarding the importance of a sustainable growth strategy. Even in times of volatile and uncertain economic conditions, the world still continues to change around us: Markets, business models, manufacturing processes and other challenges along the value chain are all changing at an increasing speed in an increasingly interconnected world where new opportunities and threats appear constantly.
Some of the drivers behind these changes are so-called megatrends, which result in far-reaching processes of transformation across regions and industries. More value is added by KPMG expert opinions who present crisp, quick and relevant reflections on these hot trends. "The manufacturer of the future must take these megatrends into account in order to remain competitive, create value for its investors and secure its position as a partner of choice for its customers and other stakeholders," Dr. Gerhard Dauner, Partner, Head of Industrial Manufacturing Europe, Middle East and Africa
Trend 1
Factory of the Future
Manufacturing companies are adapting more and more digital technologies to network and transform their manufacturing processes. The "factory of the future" can be broadly defined as a future view of an interconnected manufacturing value chain, involving information and communications technology (ICT) and automation technologies: Software will holistically interconnect and manage distributed factory assets.
Embedded data collectors in processing centers will be linked to cross-functional enterprise systems, enabling real-time two-way data exchange and full production quality control. In the "factory of the future", the adaption of various digital technologies will also enable the data exchange from R&D (CAD, virtual simulation tools, rapid prototyping) to the factory floor (automation/robotics, control technologies, product lifecycle management (PLM), additive manufacturing) to distribution partners (analytical applications) and back, from suppliers to OEMs to customers, and vice versa.
"Through IT information systems that are fully-integrated from customers to suppliers, future factories and their supply chain will be directly driven by the customer. Transparent measurement of all significant process steps will allow a fast reaction to all deviations. The factory has to deliver reliable processes and highly skilled people who are able to follow the fast-changing demands of customers and markets." - Michael Bremicker, Partner, Consulting - Supply Chain Management & Procurement
(Continued on the next page)