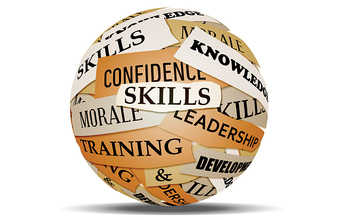
Narrating Solar Industries' plans, Dwivedi mentions, "We have already initiated the Competency Mapping initiative (through Assessment & Development Centres). Using best available tools for Assessment and Development Centres we have come up with the Action plan, which will lead us to the further Areas of Development. In next phase, we will undergo the Impact assessment of the activity done. All these activities are inspired by The Deming's principle (Plan-Do-Check-Act)."
In this efforts of skill development, creating conducive work environment is equally important. Speaking about the initiatives and processes at Toshiba India, Okada says, "In a manufacturing set up, to achieve time efficiency, entire process is divided into multiple production lines. While each engineer and employee is responsible for the quality of the product that passes through his/her production line, to assure high quality of the end product teamwork within the whole factory is paramount. We encourage our employees to effectively work together as a team. Realizing the competence and capability of our Indian engineers and technical staff, our endeavour is to constantly enhance and upgrade their skills and build quality consciousness in them and infuse the feeling of commitment and teamwork."
Industry Academia relation
The Government of India is also taking steps to upskill the youth and make them industry ready. Narrating the various initiatives, Anbu highlights that through the National Skill Development Corporation, Government of India has been training engineers. "The Ministry is also supporting development efforts in IoT, Industry 4.0, advanced manufacturing, etc. Industry bodies and associations such as IMTMA are creating a conducive environment to train workforce in these applications through their various training programmes conducted at their Tech Centres in Bengaluru, Pune and Gurugram. IMTMA conducts industry awareness workshops at colleges for students to make them industry ready," he adds. However this is not possible without the industry's help.
Toshiba India is also supporting the ‘Skill India' initiative by imparting technical skill training to Indian engineering students. "We conduct periodic training programs for the students of ITI (Industrial Training Institute) at our Toshiba JSW factory in Chennai," informs Okada. Similarly, there are other companies as well which work along with ITIs. Speaking about Volkswagen India's initiatives, Dr. Lauermann says, "We are training the trainers at ITIs, introducing technical syllabus that is relevant to changing times and have even adopted one ITI in Pimpri Chinchwad to turn it into a centre of excellence." Godrej Appliances is also on the board of four ITIs in Mumbai and in districts surrounding its manufacturing facilities in Mohali and Shirwal. The company is instrumental in developing the curriculum for refrigeration and air conditioning trade. "We also work closely with the ITIs providing them with industry insights and curricular reforms that are relevant to today's practices," explains Shariyarr.
Elaborating further on the company's other initiatives, Shariyarr he asserts, "Under the vocational training program of the group's ‘Godrej Disha' initiative, we address this skilling gap by providing high quality vocational training in collaboration with renowned training institutes. ‘Godrej Vocation Training Schools (GVTS) initiated as far back as 2012, and has successfully trained over 37,000 students."
(Continued on next page)