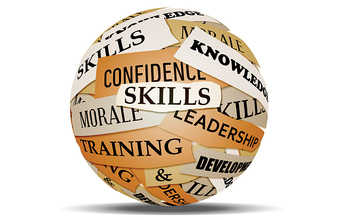
Wabco India also undertakes training for their employees. In this regard, Kaniappan recited the efforts that the company takes. "We constantly anticipate and track the evolving industry trends both in India and global markets and through our structured talent management program; we are able build a strong talent pipeline with the required skill sets. Talent management is done in every function with a view to identify top talents, prepare a succession plan and formulate developmental action for the identified talent. Moreover, as a part of the talent management process we regularly implement talent and skill development actions like benchmark visits to customers, suppliers and other manufacturing organizations to learn best practices, structured job rotation, short term training programs, higher education programs, participation in industry forums conducted by industry bodies like ACMA and CII, six sigma green belt programs and short term assignments at other global WABCO locations."
Speaking on Solar Industries' efforts, Dwivedi notes, "As far as existing employee are concerned, we have launched Competency Mapping initiatives (through Assessment and development Centres), which leads us to the clear picture about the existing Skills & Competencies available. After Competencies are identified then comes the next phase of Coaching and mentoring through the Learning and development Models."
Similarly, Toshiba India has its own initiatives for its employees. Explaining the same, Tomohiko Okada Managing Director, Toshiba India Pvt. Ltd. says, "Maintaining high Toshiba quality standards, at par with Made in Japan products, across all our manufacturing plants around the globe, is one of our key objectives. To achieve that, technical training is an integral part of employee development at Toshiba. We have training programs for engineers wherein Indian engineers are taken to our facilities in Japan to get them acquainted with the latest technologies, manufacturing processes and skills. Engineers from Japan also regularly visit the manufacturing facilities in India to supervise, support and train the local engineers. We also send our employees to visit manufacturing plants in Japan for skill development and advanced technology training."
"At Godrej Appliances, we indulge in a multi-pronged approach to bridge the skill gap: Investing in in-house training programs - through our technical training centres at our manufacturing locations, we upgrade the skills of our workforce for our requirements. The technicians and operators are trained on the new technologies through class room inputs and practical training on models and simulators. This improves their knowledge and builds confidence. For skill development in software programming, both managers and operators are also sent for training to Siemens, Fanuc, etc. When new equipment with new technology are introduced, the operation and maintenance team are trained by the OEM at their factory and at our factory," describes Shariyarr.
Kaniappan further says that to develop a competent workforce, Wabco India imparts need based trainings to the operators, with emphasis on quality for multi skills and involve all employees for the improvements through suggestions scheme and QCC projects. "Structured training on specialization & analytical skills is regularly conducted and Total Productive Maintenance (TPM) is used and leveraged as an effective tool to improve overall productivity," he reveals.
(Continued on neat page)