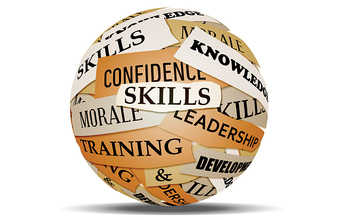
Analysing the situation, Hari Prakash M, CEO, GP Petroleums says, "It is understood from various sources that only 2 percent of Indian labour force is skilled against the highest 96 percent in Korea, Japan 80 percent, Germany 75 percent and China 40 percent. Based on our observation - a) Production department & b) maintenance department faces real challenge with skilled labour requirements. India is amongst
the young countries because close to 30 percent of its population is youth with literacy percentage is almost close to 75 percent. By this data, it is learnt that the progress of any country lies with skilled labour and for country like India where the skilled labour set is very low, has tremendous potential and opportunity to offer skill based trainings to make the future strong and supply skilled labour not only to Indian manufacturing industries but also overseas industries."
Seconding the same, P. Kaniappan, Managing Director, WABCO India Ltd. mentions, "Attracting top talent to the manufacturing industry is always difficult. To overcome this challenge we have launched our specially designed PACE maker program and Great Place to Work initiatives to help us attract the best talent."
Taking a different perspective, Shirin Salis, Vice President—Human Resources, Ingersoll Rand India believes, "The challenge that the manufacturing industry will need to overcome is the negative perception that it suffers from- that it comprises of mostly unskilled and partly skilled workforce while the actual skill demands of the industry are ever increasing in the face of digitalization. Mapping critical skill sets to roles and functions, redefining the employee value proposition and opportunities for career progression are critical to manage the sourcing and developing of critical skills required by the industry. Additionally, there is dearth of talent in the industry, which needs to be addressed on priority. However core engineering and manufacturing management skills are available in our country, but they need to be honed further to keep abreast with the changing functionality of manufacturing. Furthermore in today's rapidly changing scenario, it is next to impossible to find the ‘right fit' for the ‘right role'. Therefore organizations need to be ready to cultivate and nurture inhouse
talent to fuel their long term growth."
Employee training
India's manufacturing industry is moving towards Industry 4.0 to keep itself at par with global competition. Elaborating on the same, Salin continues, "Increasingly, new-age and futuristic technologies such as artificial intelligence, machine learning, big data analytics, artificial intelligence, internet of things, block chain, etc. are changing the talent landscape. Manufacturing processes now need employees with high-tech skill set, proficient in mathematics and possessing an analytical mind-set. In the wake of these developments, it is a significant priority for organizations to upskill their workforce at a rapid pace and transform their workforce with the evolving manufacturing ecosystem. Organizations with a thriving talent pool will be the ones winning the manufacturing race in the near future."
Agreeing to it, Anbu opines, "The workforce needs to be educated and trained in understanding the new technologies. The skill sets of the engineers in new technologies need to be enhanced so that they could put technologies."
In this regard, Volkswagen India focuses on skilling at various levels to cope up with the rapidly transforming industry. "We undertake special training programs for the employees," says Dr. Andreas Lauermann, President & Managing Director, Volkswagen India Pvt. Ltd.
(Continued on next page)