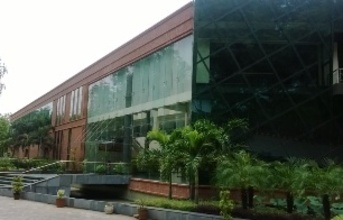
About the plant
Kalol Plant
Plot area: 72500 sq. m.
Built-up area: 19000 sq. m.
Plant operational since: 1982
Key clients: Tata Motors, Bharat Benz, Ashok Leyland, MAN India, Mahindra & Mahindra, Volvo - Eicher Commercial Vehicles and Asia Motor Works amongst others.
Certifications: TS 16949, ISO 14001, OSHAS 18001 and VDA 6.3.
Key supply chain partners: RBD, SSS, Valeo, ASPL, Schaeffler Group - FAG, Asian Tubes.
Key green features: Only EMS - OHSAS certified Clutch Company.
Products
Key Products manufactured: Clutches: Friction Type dry clutch
Operation wise (Pull Type/ Push Type)
Material Wise (Ceramic /Organic etc.)
Dia. wise (170/280/310/352/380/385/395/400/430 etc) (in mm)
Exports models: 352,385,395,400,430 (dia. in mm)
OE: 310/352/380/395/430 etc
Indian After Market: 170/310/352/380/395/400/430 (Dia in mm)
Coil Spring Type (Axial/Angular)
Diaphragm Type.
Capacity: 30000DP + 60000CA / month - Kalol, 3 shift basis;
Manufacturing principle
Setco Automotive's Kalol plant has been adopting and practicing lean manufacturing. The emphasis is on cellular and one piece flow assembly lines with focus on waste reduction as well as continuous improvement in the manufacturing practices. "Having an environment that promotes safe working as well as encourages employee engagement is an integral part of the Setco philosophy," Sheth says. Across all its plants, Setco follows stringent quality checks at supplier end, incoming stage, in process checks and the final stage to maintain supply of zero defect products to its customers.
Key technological features
• Semi - Automatic / manual type operations in production shops.
• Computerized Comprehensive testing machines at the end of line to certify the functionality of products.
• Quality Lab with key critical machinery like CMM, Profile projector digital / good quality gauges.
• NPD department in-development proto shop with state of the art validation lab having all functional testing in-house facilities.
• Semi-Automatic CNC shops with VMS and CNC machine lathes by Fanuc, Siemens.
• Old-school machinery equipped machine shop too, with the same for conventional mechanical chores on sub-components.
• Press shop equipped with range from 1000T to 160 T mechanical and semi-automatic presses.
• Heat treatment consisting of SQF and IPSEN furnaces equipped with SKADA software as well as a in-house phosphating plant.
• A newly developed in-house Diaphragm production plant.
• In-house Metallurgical Department for inspection and testing of material for clutches with all testing machines like UTM, spectrometer, Microscope, micro Vickers hardness tester.
• R&D Department, with 24*7 Endurance Testing machine Lab and performance testing Lab with machines like Hysteresis and Parameters Testing machines, Burst testing machines and performance parameters testers.
• Dynamo testing Machine and Clutch Actuation Model for both automatically and manually testing the product, respectively.
(Continued on the next page)