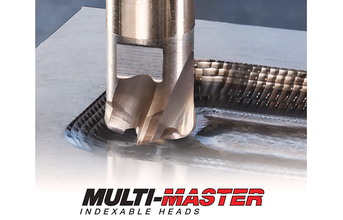
For ISCAR, as for any cutting tool manufacturer, die and mold making is a highly important customer segment. This industrial branch not only consumes more and more tools but constantly puts forward new demands, which have a significant impact on advances in cutting tools. These demands are typical for every metalworking sector: the customer is always interested in more productive, reliable, and accurate tools. However, specific features of die and mold manufacturing necessitate special design considerations beyond the general requirements. Materials, machined shapes, and machining strategies are three distinctive hallmarks of die and mold making, and have a substantial influence on cutting tool demands. According to ISCAR, only a holistic tool development concept based on these features, combined with integration of Industry 4.0-inspired digitalization developments, will lead to successful solutions for the die & mold sector.
Challenging Materials
The main material for the die & mold industry is steel that is often hard. Workpiece hardness is a principal factor in influencing tool material and cutting geometry. Various repair methods for worn or damaged molds and dies use welding, thermal metal spraying, and laser treatment, etc., which are applied to the affected surfaces. Further machining of these surfaces requires a cutting tool to remove a material stock combining very hard and relatively soft layers. This condition significantly reduces tool life and requires tool manufacturers to make extra efforts to compensate and ensure the necessary durability.
Intricate shapes
Molds and dies feature complex shapes. A three-dimensional (3D) profile is typical for the working surfaces of a mold (die) set, and the ability to machine 3D surfaces effectively is an important requirement for cutting tools. A tool is expected to provide the required parameters for shape accuracy and surface finish, and to ensure the appropriate level of tool life needed to complete machining the shape or its pattern in one operation.
Machining
Manufacturing molds and dies requires various machining processes: turning, milling, drilling, reaming and others, although cutting tools for die and mold making are associated primarily with mills. The specific character of the die & mold industry - predominance of non-rotating parts, the complex shape of machined surfaces, the necessity to produce a lot of cavities that require considerable material stock removal, etc. - positions milling cutters in the first place among tools utilized by this branch.
In their constant need to boost productivity in manufacturing molds and dies for new products, the die & mold industry was one of the first adopters of advanced machining methods such as high speed milling (HSM) and high feed milling (HFM), and to develop efficient machining strategies.
The progressive methods and techniques that were introduced impacted greatly on cutting tools, leading to new requirements for tool manufacturers. Over the years, these requirements have become increasingly tighter; today die and mold makers represent one of the most exacting cutting tool consumers and expect cutting tool manufacturers to be responsive to the industrial trends.
ISCAR has cooperated successfully with the die & mold industry over the years, and constantly improves its solutions for die and mold manufacturing by introducing new products and upgrading the existing ones, as well as providing complex tooling projects and consultations.
Cutting tool grades
In die and mold making, indexable extended flute (also referenced as long-edge) milling cutters are often applied to rough machining cavities and wide edges. The cutters work in high-load conditions, and the material of the indexable insert is a key factor for improving tool life. In the last few years ISCAR has introduced IC845, a cemented carbide grade that features a new tough substrate and a new nanolayer PVD coating with applied SUMO TEC post-coating treatment technology. The grade was designed especially for cutting at significant impact load. The inserts made from IC845 demonstrate substantially better tool life, which in turn improves performance of the extended flute cutters and slot milling cutters carrying the inserts.
ISCAR's solid carbide endmill line has been enhanced by adding the IC702 carbide grade, which is intended for efficient machining of hard materials (up to HRC 65).
Advanced profiling
In machining complex surfaces, the real workhorses are milling cutters of toroidal- (button-) and ball-nose shapes. ISCAR offers die and mold makers an extensive line of these cutters in the following designs: tools with indexable inserts, endmills with exchangeable cutting heads, and solid carbide endmills. They differ in nominal sizes, accuracy, mounting method (shank- or arbor-type) and application range, according to whether the workpiece hardness is low, moderate or hard.
Mold and die making is characterized by a large proportion of small- and medium-size producers. For these manufacturers, tool versatility (multifunctionality) is an important factors in tool choice.
ISCAR's recent LOGIQ campaign introduced a new product targeted especially to this challenging market - the TOR6MILL family of indexable milling cutters. A TOR6MILL cutter (Fig. 1) can carry inserts in four different geometries. Mounting the appropriate insert in the cutter transforms it to a toroidal, 90°, 45° or high feed milling tool. The cutter can be applied to machining 3D surfaces, square shoulders, plane faces, chamfers, or use as a productive high feed rougher.
Innovative technologies
High feed milling and high speed milling proved to be powerful methods for dramatically increasing machining productivity while reducing manual operations, consequently shortening production time significantly. Due in no small part to timely introduction of these efficient methods, the die & mold industry succeeded in filling the sharply increased demands for molds and dies that occurred in the 1990's.
High Feed Milling
Today, cutting tool producers provide a great choice of high feed milling cutters, and ISCAR's range of high feed (also known as fast feed or FF) milling tools seems to be the widest. ISCAR's standard high feed milling line comprises more than 10 tool families that differ in their design principle (indexable, solid, with replaceable heads), nominal diameter, cutting geometry, mounting method and applicability (machining faces, pockets, deep cavities). This diverse range enables die and mold makers to select the optimal cutter for their needs.
ISCAR views high feed milling tools as important productivity boosters and continues to develop the line by introducing new families and improving the existing ones. Not surprisingly, the leading milling products presented in ISCAR's recent LOGIQ cutting tool marketing campaign were related directly to fast feed cutters.
NAN3FEED and MICRO3FEED, two of the latest ISCAR families of indexable high feed milling tools, feature an 8-16 mm (.315-.625 in) diameter range. Even though solid carbide endmills traditionally dominate this range, ISCAR's specialists believe that the advantages of the indexable-insert concept for rough machining will position the families as serious cost-effective alternatives to the solid carbide designs.
The LOGIQ4FEED family of fast feed cutters (Fig. 2) features "bone-shape" double-sided inserts. This unusual insert profile provides four cutting edges, with an exceptional ramp-down capability that defines the main application of the family: high-efficiency rough milling of cavities, particularly deep cavities.
The cutters are suitable for machining workpieces with hardness up to HRC 50.
High Speed Milling
Expanding the range of products intended for high speed milling, ISCAR introduced multi-flute solid carbide endmills in 2 - 20 mm diameters (.250-.750 in) for high speed finish and semi-finish milling. The endmills are produced from the ultrafine IC902 carbide grade, which was developed to machine hard materials, and have a cutting-length-to-diameter ratio of up to 6. They are operated at rotational speeds up to 20000 rpm. The application of solid carbide endmills for rough milling of slots and open pockets - by trochoidal technique and at high metal removal rate (MRR) - has also reached the attention of die and mold makers.
MULTI-MASTER options
The need to customize molds and dies to products is why die and mold manufacturing is often low-volume or even single-piece, which results in a large number of small- to medium-size shops involved in die and mold making. For these manufacturers, efficient utilization of cutting tools and wellrun tool stock management is of key importance. However, customization often requires a specific tool configuration in order to machine hard-to-reach part areas. Not every cutting tool in a tool stock is optimal for this type of machining but "customizing" the tool by ordering a tailor-made design is far from the best solution.
ISCAR's MULTI-MASTER (Fig.3) family of assembled tools with exchangeable cutting heads helps to overcome these difficulties. According to the MULTI-MASTER concept, the head is suitable for mounting in different tool bodies (shanks), and the shank can carry different heads. The heads are varied in shape, cutting geometry and sizes and are designed for machining 3D surfaces and shoulders, faces and slots, chamfers and holes. The cylindrical and taper-neck shanks feature different dimensions for a broad-ranging overhang; their design options ensure clamping in toolholders, collet chucks or in a machine tool spindle directly.
The MULTI-MASTER, with its rich variety of heads, shanks, reducers and extensions, enables over 40,000 possible tool configurations. The MULTI-MASTER tools wholly meet the requirements of the important "no-setup time" principle, as replacing a worn head does not require additional setup operations. The head can be changed without removing a tool from a machine, which significantly decreases downtime. These features make the MULTI-ASTER family extremely popular in the die & mold industry.
Digital tool assembly
The low-volume character of die and mold manufacturing and highly precise machined shapes make any deviation from die (mold) specifications an Achilles heel. Even a small error threatens rejecting a whole product. Driven by Industry 4.0 developments, digitalization in modern manufacturing is providing die and mold makers with an effective instrument for overcoming this obstacle - computer modelling of machining processes. This ensures the implementation of productive machining strategies, tool path and cutting data optimization, and prevention of possible collisions.
ISCAR expanded its world of digitalization by introducing a milling tool assemblies option in its electronic catalog, which contains accessible and accurate tool data for digital pre-machining. Creating a digital tool representation of a tool assembly, based on standard ISO 13399, facilitates accurate communication of tool information between software systems. Integrating this new function into the CAD/CAM system of a die and mold manufacturer can prevent errors on the shop floor during machining, while the ability to plan multiple assemblies saves time and costs in the planning process. The company plans to expand its Industry 4.0 data-driven products and to connect the digital and virtual worlds of modern manufacturing for die and mold makers.
Many products around us are manufactured using molds and dies, and demand for these products grows constantly. Advances in industrial branches such as the automotive industry, a leading consumer of molds and dies, have a great impact on die and mold making. More requests for molds and dies will lead to a new level of requirements for the cutting tools that die and mold makers need. ISCAR holds that cutting tool manufacturers should anticipate these demands and act accordingly by providing the necessary solutions.
Source: ISCAR