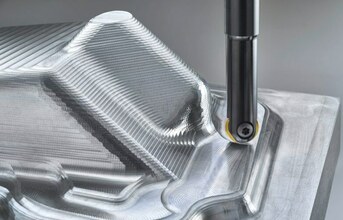
Save money Cost-effective roughing depends on one thing: The maximum possible material removal rate. For modern machining centers, this doesn't just presume innovative milling tools rather it also requires a selection of cutting materials for modern materials. However, these requirements are not a problem for the two new MultiFace H45 PRO4 (figure 2) and MultiFace P45 PRO8 face-milling cutters from LMT Fette. The inserts of the first version are set up high-positive and have four cutting edges. The second version has positive turning inserts with eight cutting edges each. These tool geometries markedly reduce the spindle load. Even on low-power machines, it is possible to achieve large material removal rates. This saves production time and machine costs and conserves resources.
figure 2
In the practical application, machining has been taken to a new level. In the face-milling of a copper block, different requirements were clearly exceeded. Due to the low power consumption of the high-positive version, it was possible to increase the diameter of the tool used from 100 mm to 160 mm and thus increase the radial infeed ae to 102 mm - previously it was 48 mm. Using optimized cutting values it was possible to more than double the material removal rate to 676 cm³/min. The service life per cutting edge also increased from 18 hours to 24 hours, meaning that wear didn't stand a chance.
Maximum toughness The efficient machining of hardened and high-strength materials is a particular challenge for cutting tools. Both the demand for long service life and the maximization of removal rates are rapidly driving development to its limits. But this is not true of the MultiEdge 2Feed mini high-feed cutter from LMT Fette. New indexable inserts complement the range of already established milling tools.
A special carbide substrate combined with a TiAlN-based high-performance coating easily overcomes material hardness, material strength and comparable competitors' products. The tried-and-trusted high-feed geometry of the 9 mm small inserts for infeed depths up to a maximum of 1 mm with a thickness of 3 mm allow for a veritable flood of chips during roughing. The slightly positive angle of attack of the indexable inserts also makes a decisive contribution.
In practice, this leads to a considerable reduction in machining times. During the high-feed machining of highly tempered steel 1.2343, it was possible to halve the machining time compared to a competitor's tool. The long service life of 165 minutes also contributes to reducing costs. The MultiEdge 2Feed mini works very reliably and economically, even with large projection lengths.
(Continued on next page)