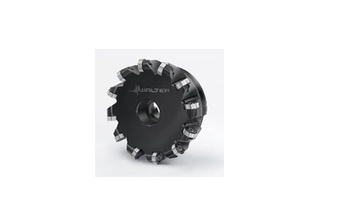
16 cutting edges reduce the pressure on the workpiece
Further saving measures: Walter uses identical indexable inserts with 16 cutting edges as semi-finishing and finishing inserts. Previously, the market standard was to use twelve for semi-finishing and four for finishing. This also simplifies inventories and eliminates errors when changing the indexable inserts.
The indexable inserts are coated with PVD or CVD and are available in various geometries. Indexable inserts belonging to the Walter WSP45S or WSM45X grades are typically used. Short cutting edges reduce the pressure on the unstable components. This results in reduced vibration, which improves surface quality, increasing it from the usual Rz 7-8 to approx. Rz 5. "Overall, these measures lead to improvements in handling and process reliability," says Buob.
As a rule, every third to fifth insert is positioned differently on the finishing tool. The position of the semi-finishing inserts can be adjusted by approximately 5° in the same way as when carrying out rough machining; the finishing inserts are inserted so as to cut in a flat plane. Rolf Buob explains: "This is why we distinguish between semi-finishing and finishing inserts on the same tool, even when the inserts are identical. Only the insert seats are rotated differently when inserted."
The cutting speed when finishing is approximately 140 m/min at a feed rate per revolution of up to 4 mm. This milling cutter is also available for machining allowances of up to 3 mm for roughing in particular. Here, the indexable inserts are aligned uniformly both axially and radially, in contrast to the finishing face mill. They all have the same function for machining operations.
However, the new milling cutter concept does not mean that development has finished. Walter is expected to make further advances involving new PVD coatings that are currently still in development.
END
SOurce: Walter AG