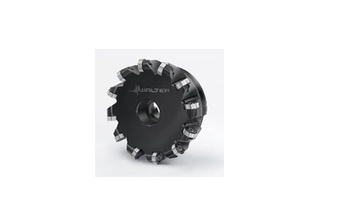
Reducing machining costs
"We expect - and studies by leading turbocharger manufacturers agree - that the number of turbochargers used for petrol engines will experience a 2.5-fold increase over the next five years," says Rolf Buob, Component Manager for turbine housings at Walter AG in Tübingen.
Currently, turbochargers for petrol engines place particularly high demands on machining when compared with diesel engines. The exhaust gases in the turbine housing reach temperatures of between 1000 and 1050 °C; in diesel engines, however, they reach relatively low temperatures of between 800 and 850 °C.
"Temperatures of 1000 °C or higher require high temperature-resistant steels, typically chrome-nickel alloy steels that have a material identification number beginning with 1.48 and ending in 49, 48, 37 or 26 - with a tendency towards the material identification number 1.4826. These 1.48 steels are constantly being developed further and it is becoming more and more difficult to machine them," explains Buob.
(Continued on the next page)