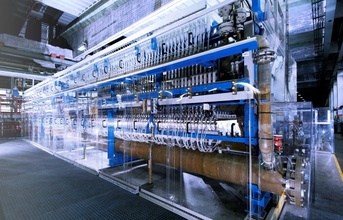
Energy consumption makes up roughly one third of the operating expenses of a chlor-alkali production plant. Thus, the advanced NaCl-ODC technology helps to significantly reduce energy costs. Compared with the conventional single-element design, it will cut CO2 emissions of the Tarragona plant by around 22,000 metric tons per year. That's roughly the amount produced by 15,000 cars in one year. Implementation of NaCl-ODC electrolysis as standard technology for chlorine production around the world would mean an energy saving potential of 35 million megawatt hours per year.
Cost-efficient solution for the chlor-alkali industry
The original NaCl-ODC electrolysis was developed by combining two key technologies: The oxygen-depolarized cathodes developed by Covestro were integrated into the electrolysis cells (single element technology) from thyssenkrupp Uhde Chlorine Engineers. By introducing oxygen into the cathode, the often unwanted formation of hydrogen is suppressed. The reaction is comparable to fuel cells, but here it lowers the electrical energy consumption instead of producing energy. This enables huge energy savings, which are highest when oxygen is available on site.
thyssenkrupp successfully commissioned the first large-scale reference for this technology at the end of 2015 for BEFAR Group in China. Denis Krude, CEO of thyssenkrupp Uhde Chlorine Engineers: "Customers expect us to supply solutions that are viable, future-proof and at the same time environmentally friendly. Our energy-saving ODC technology can make a key contribution to the competitiveness of our customers in the chemical industry. The first large-scale plant in China successfully demonstrated that the technology makes chlorine production much more eco-friendly and cost-efficient."
END