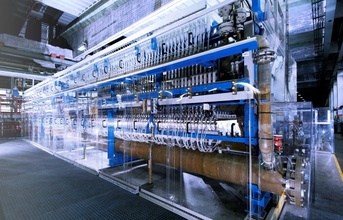
Around 70 percent of all chemical products use chlorine in their manufacturing process. At the same time, the production of this important base chemical is one of the most energy-intensive processes in the chemical industry. In order to change that, thyssenkrupp is offering the NaCl-ODC electrolysis technology (ODC = oxygen depolarized cathode) which lowers power consumption and indirect CO2 emissions by up to 25 percent compared to standard production processes.
Engineers from thyssenkrupp have now been able to develop the technology even further: By raising the current density of the electrolyzer from 4 to 6 kilo amperes, output was increased by 50 percent. Electrolyzers with the same output capacity can now be built about one third smaller, resulting in significantly lower total cost of ownership. Plant operators profit from a smaller plant footprint, lower maintenance and from the generally high efficiency that comes with the NaCl-ODC electrolysis process.
Advanced ODC technology reduces carbon footprint of chlorine production plants
thyssenkrupp's cooperation partner Covestro will be the first to utilize the advanced ODC electrolysis for a new chlor-alkali plant in Tarragona, Spain. "Three factors played a vital role in choosing the technology for our process: sustainability, energy efficiency, and increasing our site's competitiveness", states Dr. Klaus Schäfer, Chief Technology Officer at Covestro.
(Continued on next page)