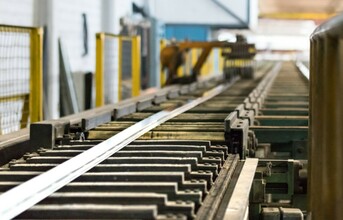
Light-weighting plays a vital role in making vehicles safer and lowering emissions. Made possible by technology and new-age material, light-weighting presents an effective way to achieve energy consumption reduction and performance enhancement. Many sectors have well accepted and utilised this concept, especially in electric vehicles, aircraft or aerospace components and system design. Being lighter is better in many applications for various reasons. The less energy used in manufacturing means that products turn out to be more environmentally friendly. The lighter the product would mean it also requires less fuel for transportation, reducing costs for both manufacturers and consumers.
Choice of Material
As environmental legislation is being worked out globally, any metal that makes light-weighting possible has become a crucial element in industries like automotive and aviation-aerospace. As country after country begin to commit themselves to reducing their carbon footprint and contain emission levels, manufacturers in these sectors have been looking at lighter yet stronger products. Research and development efforts to increase the efficiency of vehicles for improved safety, better performance standards, and higher resistance to natural damage like corrosion are ongoing. Aluminium fulfils this industry aspiration and presents itself as the metal of choice to the industry.
As the world gears up for a cleaner tomorrow, aluminium is recognised as a metal of the present and future. For the transport and mobility sector, both in road transport, where electric vehicles are emerging as the next big thing and in aviation and aerospace applications, light-weighting has become a critical requirement. In the automotive sector, the traditional way of reducing vehicle weight has been the method of downsizing. The past two decades have seen the weight of vehicles undergo a drastic change in terms of reduction.
Aluminium is now the second-most common material used by automakers world-over. Studies of the European Aluminium Association have shown that aluminium applications can help reduce vehicle weight by up to 40 per cent without compromising the vehicle's safety. It is also established that savings of 4.3 more kilometres per litre or approximately 10 per cent more in fuel economy can be achieved through light-weighting applications using aluminium. Overall, car components made of aluminium are anywhere between 10-40 per cent lighter than traditional materials.
In India, light-weighting is at a crucial stage to meet the challenges set by the government. As per the government's vision, it intends to ensure 100 per cent electrification of public transport and 40 per cent of personal mobility by 2030. As battery electric vehicles are being termed as the future of the passenger vehicle, questions of how much light-weighting will be necessary are being asked. Being heavy on weight is a demerit for the overall safety profile of an automobile, especially an electric vehicle. Light-weighting essentially drives the range and performance of an electric vehicle. In this context, aluminium alloys have helped vehicles increase range and load capacity, thus reducing range anxiety among buyers.
Another area where light-weighting capabilities are much sought after is aviation and aerospace. Aluminium alloys have reduced aircraft manufacturing costs with better fuel efficiency and handling. The future and development of new generation aluminium alloys lie in innovation, and it is innovation using aluminium that has resulted in safer and more reliable flights.
As manufacturers take on the challenge, update their designs, streamline production while factoring in maintenance and repair processes in aviation and aerospace, the results are being seen. Light-weighting for a Boeing 787, new-generation aircraft, ensured a 20 per cent weight savings resulting in a 10-12 per cent improvement in fuel efficiency. Besides a reduction of carbon footprint, improvement in-flight performance parameters like better acceleration, higher structural strength and stiffness, superior safety performance could also be achieved by lightweight design. It offers numerous advantages that are likely to continue to precipitate the increased lightweight metal and other material use.
Beyond Light-weighting
Being the engineering material of choice for various applications comes almost naturally. The principle of a lightweight design is to use less material with lower density while ensuring the same or enhanced technical performance. When aluminium is used, it goes beyond just light-weighting; it is a highly versatile metal with its advantages. Aluminium is also recognised for being flexible, offering a high strength-to-weight ratio, being resilient and ductile at low temperatures. Another crucial advantage of this metal is that a thin oxidised film forms on its surface when exposed to air, protecting it from corrosion.
Aluminium does not gather rust like steel, and even if scratched, this layer of the film quickly develops itself retaining the protection. This also makes it a favoured metal in the construction industry, in building fenestration, household utensils, or as packaging material, given that it is also non-toxic. In all of these aluminium uses, the product's weight plays an equally important role.
Looking ahead, light-weighting efforts using aluminium alloys will only continue to grow. The use of lightweight vehicles and new-age aircraft will continue to provide a practical solution for reduced fuel cost and reduced CO2 emissions. With commitments to reduce CO2 emissions only growing internationally, the use of a researched material like aluminium is set to prove further that it is the best ingredient for across industries in the times to come.