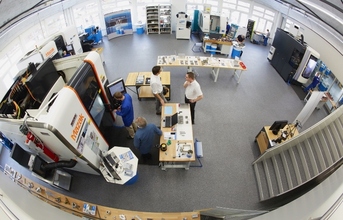
In order to be able to offer customers an effective added value when it comes to machining, the company inaugurated its very own Technology Centre in 2009. Marc Blaser: "Our Technology Centre is truly state-of-the-art and enables us to carry out stringent tests on new metalworking products and system solutions.
It also ensures that we are able to work in partnership with customers helping them improve their productivity, economic efficiencies and machining quality by identifying and developing metalworking fluid solutions that are tailored exactly to their needs, which we call a Liquid Tool. "The ability to work collaboratively and consultatively with customers is a key strength of ours, and the continued investment in our research and development facilities provides us with distinct technical (and competitive) advantages."
Doubling of the tool life
In a recent project, Blaser experts in the Technology Centre impressively optimised the tool life. A renowned partner filled the role of international supplier and manufactured vehicle parts from a high-strength titanium alloy. In the ultra-modern Technology Centre in Hasle-Rüegsau, a range of tests were started with the goal of optimising the tool life during pocket machining.
The specialists at Blaser reproduced the partner's machining environment and employed the same machining parameters and data using a DMG Mori DMU 65 mono block machining centre, and began comprehensive tests employing trochoidal milling strategies.
The tests compared machining performance (specifically tool wear) when using a conventional metalworking fluid against an optimal metalworking fluid specifically adapted to the partner's needs. The series of width of wear tests were conducted up to 0.30 mm.
The results were excellent. Using the optimally adapted coolant from Blaser Swisslube, 11 instead of just five pockets could be milled until the wear on the tool forced the processing to be stopped. The result achieved was confirmed in various series of tests, and corresponds to a doubling of the tool life.
END