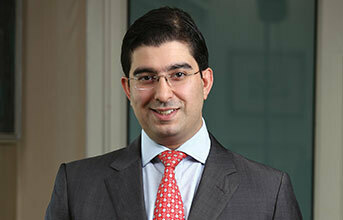
Nikhil Sawhney, VCMD, Triveni Turbines
Could you provide an overview of the Indian steam turbine market and the demand it is witnessing from other industries?
In 2022, the Indian sub-100 MW Steam Turbine market experienced a 15 per cent growth in terms of megawatts when compared to the figures from 2021. This increase can be attributed to the increase in demand for combined heat and power (CHP) within the industrial sector, which saw the market bouncing back to 2019 levels. The concept of combined heat and power involves the efficient utilisation of surplus steam generated by the turbine in various industrial processes. Furthermore, power produced through this method boasts a cost reduction of 14-15 per cent in comparison to power generated by Independent Power Plants (IPPs).
The Bio-Power industry plays a crucial role in converting diverse potential feedstocks, such as biomass, wood pellets, bagasse, sugarcane residues, and palm oil residues, into solid fuels. CHP or cogeneration plants possess the capacity to harness sustainable thermal resources, such as bagasse-based biomass fuel, to produce low-pressure steam. This steam is generated through extraction steam turbines and serves the dual purpose of generating heat and electricity.
The drive to harness locally available biomass resources, including agricultural and forest residues, has facilitated the generation of power in closer proximity to the point of consumption. Consequently, this has paved the way for the establishment of power production facilities based on biomass resources.
For an environmentally sustainable approach, thermal waste treatment, also known as incineration with energy recovery, provides a viable alternative method. The Waste-to-Energy (WtE) industry encompasses a wide range of treatment technologies that transform waste into electricity, heat, fuel, or other usable materials, along with various residues.
Triveni Turbines achieved its highest-ever earnings of Rs 12,476 million in the last quarter of the fiscal year 2023. What factors contributed to this success?
Despite the uncertain global economic conditions, the company performed well in terms of securing orders throughout the fiscal year 2023. The increase in order bookings compared to the previous year can be attributed to completing orders from industrial clients first, followed by power producers, which also expanded offerings. Additionally, there was a higher demand for API drive turbines.
Furthermore, the business unit responsible for servicing turbine equipment after purchase experienced strong growth due to a significant increase in new orders. This growth has further strengthened the unit's diverse sources of revenue, which are focused on maintaining and improving turbine performance worldwide.
Could you give an insight into your most successful innovations, which have helped the brand gain its reputation? And what new can the industry expect from Triveni Turbines now?
We have achieved advancements in research and development, particularly in impulse and reaction blading technologies and high-efficiency low-pressure stages.
Our company serves a wide range of drive applications and offers tailored solutions from our API product portfolio to meet specific customer needs. These solutions include customisation options for governors, lubrication systems, bearings, and supervisory instruments.
Further, we are involved in the development of subcritical and supercritical CO2-based power generation systems. These technologies promise improved efficiency and more compact alternatives to traditional steam-Rankine cycles.
The global heat pump market is rapidly expanding due to the favourable properties of these systems. Triveni Turbines is collaborating with leading academic institutions to lead the way in developing next generation Transcritical CO2 heat pumps.
How are you incorporating digital solutions into products and services to align with the demands of today?
Our solutions include the latest versions of the SAP ERP system, Primavera for project management, Salesforce for customer relationship management, and a suite of design software tools such as PLM, PRO-E, Ansys, rotor dynamic software, CAD/CAM, and CFD packages.
On the shop floor, we have connected all CNC machines through a central programming unit, thereby eliminating the need for human intervention and minimising errors in machining program execution.
Further, all CNC machines have been equipped with IoT capabilities for real-time measurement and monitoring of manufacturing data, encompassing metrics such as Overall Equipment Efficiency (OEE) and productivity. TTL has embraced manufacturing technologies, including laser alignment for assemblies, 3D printing for prototype development, and CMM for steam path components.
Our learning centre features a Computer-Based Training (CBT) module that offers comprehensive video-based training on our products.
Continue reading on Page 2