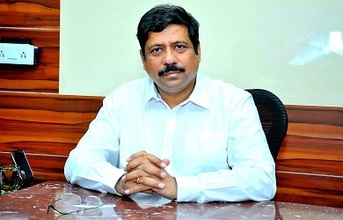
Can you give us an overview of the speciality glass/high-end glass manufacturing industry in India?
The glass industry in India is quite old and well established. It remained largely a cottage industry for a very long time. In recent years, the industry has transformed from using rudimentary mouth-blown and hand-working processes, to adopt modern processes and automation in a big way. However, Indian per capita consumption of glass packaging (1.8 kg) is much lower compared to other nations.
According to various studies, plastic will be phased out in the coming years. India's dream and global vision are to replace plastic with green and environmentally friendly glass products. Hence, the speciality glass manufacturing industry has a potentially huge demand in the present and future. We have expanded capacity to meet the rising demand, and there is no glass shortage.
As pharma bottles are non-returnable, they are produced at the lowest possible weights and with a uniform thickness, which will be an added advantage for logistics. With the help of advanced ‘blow-blow' and NNPB technologies, bottles are produced with airtight packaging and delivered to the customers. Hence, AGI is gearing up for phasing-out plastics through its innovative glass packaging solutions.
Where does AGI glaspac stand in terms of its market share and brand value in the market?
We are currently one of the leading glass manufacturers with a market share of 20 per cent. The total glass manufacturing capacity in the country is eight thousand tons per day.
What are the key challenges that the industry has been facing traditionally?
The main challenges for AGI are the speed of implementation of our plans and the uncertain government policies, which can affect the market and our customers from time to time. By 2030, only innovative companies will survive. Robotics, digitalisation, IoT, Industry 4.0, have become important these days for all companies. We believe that innovation cannot happen with one person or department. It will start with teamwork.
We have a clear policy of prioritising the domestic market and hence do not export at the cost of domestic demand. Another challenge that AGI and other manufacturers face is the perception of the western world about the products and services provided by the country. This perception will change once the companies start working with us, and we deliver the best products and services to them. Otherwise, we are on par with manufacturing facilities existing anywhere in the world.
How has the COVID-19 pandemic affected the industry in general and AGI glaspac in particular?
In the glass sector, the problems faced by the industry in this emergency period and immediately before included:
• Supply of raw materials\input for manufacture
• Transportation of finished goods
• Employees' ability to come to a place of work.
The novel coronavirus crisis has already led to some of the sharpest declines in recent times in demand for certain types of packaging, including flexible films in the snacks industry, glass and metal in the alcohol industry while accelerating growth for others—such as packaging for e-commerce shipments like flexible, rigid plastics and corrugated grocery packaging that are emerging as lifelines in this new world.
Ironically, during the pandemic lockdown situation, the demand for the food segment witnessed a rise while the demand in the pharmaceutical sector remained static. During the lockdown period, people were in their houses and less exposed to other medical services. Hence, the pharmaceutical glass bottle segment did not pick up.
However, we now plan to make vials for vaccines, including the COVID-19 vaccines currently under development by Indian biotech companies. We are in active talks with them. There is going to be a recurring demand in the vaccines space in the coming 2-3 years, which will boost the glass business.
How have you been dealing with the pandemic, and what are the key learnings that it has given?
The packaging of beverages has become quite important after COVID-19, owing to safety concerns. The glass packaging industry is seeing increased demand from the food and beverage and pharmaceutical sectors post the COVID-19 pandemic, as it has led to higher demand for medicine bottles, food jars and beverage bottles.
About 90 per cent of the glass containers are used for food and beverage packaging. The demand for glass packaging from cosmetics and perfume manufacturers also remains strong as these are luxuries that some consumers are still happy to buy.
Many glass packaging manufacturers have called on governments to ensure that regular recycling collections continue during the pandemic so that these materials can be converted into new products. Several glass-packaging manufacturers have also partnered with distilleries turning to hand sanitiser production.
Hence, AGI glaspac is striving hard to bring in the latest technologies, which will be beneficial and safe for users. Our R&D department has developed an anti-bacterial range of bottles using advanced Germ Guard and Active Silver Technology.
Key learning:
• Be ready for anything—and stay nimble
• Learn how to use technology like Zoom, Teams etc., before you really need it
• Deliver products and services in multiple formats
• Keep a cash buffer
• Have multiple revenue streams
• Always be growing.
The pandemic has also accelerated the adoption of digitalisation. What has been the case with AGI glaspac?
We are trying to implement all the best practices in manufacturing, introduce the management tools of operations and collaborate with world-class glass industries for technology transfer.
Digitalisation and automation are being introduced to improve business efficiency. AGI glaspac uses the latest technologies to integrate its R&D, production etc. We have adopted Windchill, which is a product life-cycle management tool that integrates all the stakeholders of the operations right from new product development to bottle packaging. The SAP system is in use to track everyday operations metrics and quality parameters. The business excellence team is equipped with all the tools required for effective statistical analysis and development of new methods for sustaining the improvements.
What more needs to be done to strengthen this value chain both from the domestic market perspective as well as with regards to becoming globally competitive?
Our customer base comprises a host of multinational and Indian companies catering to various business segments. The domestic market is our priority, and AGI glaspac has a clear policy that we would not like to export at the cost of domestic demand.
Tell us about the company's expansion plans of investing INR 220 crore in a new plant at Bhongir. Why did you choose Bhongir for this investment?
The Bhongir facility was established in 2009 and saw a further expansion in 2012. Through this new facility, we see a big opportunity across pharmaceuticals and biotechnology, cosmetics, perfumery, personal care and other sectors.
With the Hyderabad and Bhongir facilities put together, AGI currently melts around 1,600 tonnes of glass per day, from 80 tonnes per day capacity in 1972. We are focusing on R&D in the areas of input, processes, metallurgy and products using both in-house and external capabilities and support from across the world.
Bhongir seems like a good investment, with the Telangana government ensuring stability and being very enterprising. The bureaucracy has been supportive, and the state has ensured clarity in its industrial policies. The government has provided uninterrupted electricity, water and other amenities. There is also a lot of quality manpower available in the state. The quality of life here has helped us attract senior professionals from across the world.
What are the factors driving this expansion and growth?
AGI has positioned itself as one of the leading container glass manufacturers in the country with two manufacturing facilities. With respect to expansion, we have already invested in the upgradation our plant. Our investments are in technology upgradation, inspection, packaging systems, warehousing, and logistics. We are also looking at increasing our volumes by at least 50 per cent in the next five years.
The industry is experiencing a surge in demand, owing largely to the growing purchasing power, urbanisation, modern retail and growing awareness about health and hygiene among consumers. The industry's success is likely to continue or possibly improve even further in the future due to rising disposable income and India's GDP rate in the short- and medium-term. The local economy, which remained largely unaffected by the global financial crisis, has been a major aid for the glass container industry, allowing manufacturers to grow even during these uncertain times.
At present, what kind of manufacturing footprint do you have?
We are currently one of the leading glass manufacturers with a market share of 20 per cent. The total glass manufacturing capacity in the country is eight thousand tons per day. The speciality glass facility will have a manufacturing capacity of 154 tonnes per day and five manufacturing lines spread across 15 acres. The company foresees top line growth in its revenue by not less than 15-18 per cent by 2022-23.
What impact will the Bhongir investment have on the local economy and employment?
The company currently has a capacity of 1,000 tonnes of soda ash glass per day in the Bhongir unit and is expected to generate 4,000 jobs. Our new green facility aims to upgrade the living standards to increase society's wealth as well as the purchasing power eventually. This investment in AGI glaspac will enhance country's value in the speciality glass's global market. Additionally, it will increase productivity of domestic market by attracting the players who depend on the domestic supply chain than importing. Lastly, our vibrant manufacturing base leads to more research and development, innovation, productivity, exports, and jobs for middle-class community.
Give us an overview of your exports business.
The company exports to North America, Europe and Africa and is seeing fresh opportunities in Australia, New Zealand and regions like Canada, as well as the APAC regions.
What is your take on PM Modi's vision for ‘Atmanirbhar Bharat' from your industry's perspective?
Atmanirbhar Bharat: Atmanirbharta (self-reliance) is not just a dream, but a well thought out roadmap for a future-ready India. This move has brought all the pharma, and food companies started procuring from local industries to reduce import dependence for glass products.
Things to highlight:
• Employment opportunity to 10 lakh people (Direct and indirect)
• It will bring an investment of approximately Rs.9000 crore.
• Increase in supply in the domestic market will restrict the reuse of glass bottles in the beer and liquor industry improving the hygiene and quality of human life.
• Solar-tempered glass is an essential component promising a huge employment opportunity due to huge growth potential of renewable energy market.
• The current per capita consumption of glass at 4kg is way below the global average consumption of approximately 110kg. Rising income and affordability of glass would result in more consumption and higher demand with Atmanirbhar Bharat.
END