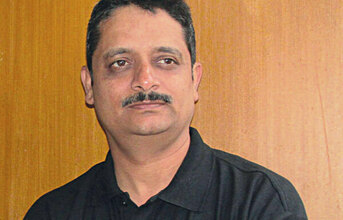
How useful is hyperMILL when creating prototypes?
Prototyping is an ongoing process and it is a very tedious job involving manpower and a lot of man hours. Our main advantages are the possibility to react very quickly - with no loss of precision and quality, because hyperMILL offers powerful CAM strategies and supports CAM changes very fast. That's why our customers save a lot of time.
Do you regularly introduce upgraded versions and new products? How does it affect customers?
We keep updating our software versions at least twice in a year and normally the available current version will be fully capable of handling any changes needed by the automotive industry. This is due to the fact that any user will not be fully utilising all the features in the CAM software and when needed we offer our online support or at site support to solve these issues or upgrades.
Most of our users are already informed online if any up gradations are available or needs to be done. Our current installed versions with latest features are far ahead with any of our competitions and innovations still going on, for e.g. Tire Mold Package is a special tailor made package and uses unique 5 axes dynamic roughing strategies.
hyperMILL millTURN CAM software: The module is completely integrated in hyperMILL
The aerospace industry requires critical components that are often complex and difficult to machine. All this needs to be done with adherence to the strictest quality norms. What role can hyperMILL play in this scenario?
Indeed, this industry is very challenging. These materials are tougher, lighter and have a very good durability. Aluminium alloys, special steels, Titanium Inconel, high temperature resistant materials and composites are already being machined for many years and many users have adopted conventional methods to machine them. There is high degree of complexity when we do rough machining and then the part goes for any external treatment and once again put back on the CNC machine. We have to be very careful in choosing the correct finishing strategy.
We have made our own experience worldwide in machining of aerospace engine parts like Blades, Impellers, bladed disks, diffuser, casings, rotors, and they need very high degree of dimensional accuracy and finish.
Let's take an example, to machine an aerospace actuator, the material is tough, with complex surface profiles and requires multiple operations and very tight dimensional and surface quality parameters. hyperMILL takes its advantage by using very innovative strategies right from roughing, semi finishing, and final finishing, to cite a few cycles like, 5 axes arbitrary roughing and finishing, rest material removal, production mode, 5 axes drilling, 3D probing, automatic rest machining, and finally collision avoidance plays a very major role as the 5axes CNC milling machine also has some limitations in simultaneous movements. Safety becomes utmost priority and hyperMILL has a very distinct advantage in this area by way of integrating Virtual Machining.
We provide well known and proven cutting strategies to achieve consistent quality. That´s why hyperMILL plays an important role in the aerospace industry.
(Continued on the next page)