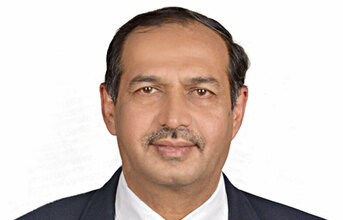
BC Rao, Kennametal
Today this technology is very effective in various applications like sawing, drilling, turning, milling and tapping. Manufacturers using MQL have tremendous advantages including better tool life, significant reduction in cutting fluids volume, reduced costs of fluid handling, decrease in the maintenance costs and increased machine up time. With the right lubricant, the right application and right machining system, it possible to increase tool life while saving money, and being environmentally responsible. We are excited to help our customers meet this challenge through our dedicated cutting tool program and expertise.
Difficult to machine work piece materials
"Necessity is the mother of invention" - No doubt, market dynamics are playing a very significant role driving the customer needs and cutting tool industry is not an exception. Machining processes become increasingly complex when it comes to difficult to machine materials primarily in aerospace, defence, power generation and oil & gas segments. As our customers' challenges change, Kennametal is there to address their machining needs with the best solutions. This is evident in our new product development, and in fact, we achieve more than 40 percent of our sales each year from new products that are less than five years old and deliver at least 20 percent productivity improvement.
Becoming a partner
Any customer who buys a Kennametal product is supported by the global Kennametal service network. In order to reduce the turnaround time, we have regional reconditioning centers for round tools in all major manufacturing locations in India.
For some of the fast moving standard products like PCD milling inserts, we do have a "Blue box" system wherein customer need not have to wait until the product sent is received back after reconditioning. Reconditioned products already available in stock will be exchanged against the quantity received from customer. This improves the turnaround time to a great extent and helps customer to manage production with less inventory. We also offer Tool Management System (TMS) and going further one step ahead we also offer "Cost per Part" (CPP) program to our customers.
We understand cutting tools and process engineering better and when we manage customer lines it actually enables to deploy proven production methods with guaranteed savings to customers. The CPP program reduces overall costs per part by managing tooling, increasing efficiency, and tracking outcomes. We guarantee a specific cost per part savings and partner with customers for long-term success. I am proud to say that we are the only one solution provider in the industry today who can deliver entire solutions ranging from special purpose machines, fixturing, process engineering and tools to our customers in India.
END