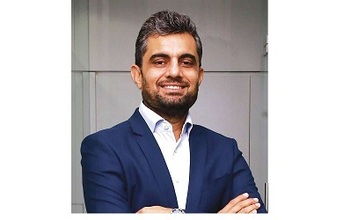
“Although the potential for future uses such as creating a fully 3D printed car is tempting, the technology has a more immediate value for car manufacturers — the ability to quickly print any component or part on demand," says Rajiv Bajaj of Stratasys
Usually, the conversation about 3D printing (Additive Manufacturing) quickly escalates to its massive potential and the amazing things we will be able to completely 3D print in the future. While it is a fascinating thought exercise, additive manufacturing is not the sci-fi technology many believe it to be, but a real application that is already making a difference across several industries.
In the automobile industry, additive manufacturing has already ingrained itself at several steps of the production line, even among Indian automakers. It may have started in the design and prototyping lab but in the past few years, 3D printing has shown its value to automakers in several ways. Although the potential for future uses such as creating a fully 3D printed car is tempting, the technology has a more immediate value for car manufacturers — the ability to quickly print any component or part on demand.
Traditionally, car parts and spare components require both production and storage costs. Over time, this means cars stop being serviced, inventory costs soar, and production must be diverted to spare parts. With the potential to solve this major pain point, 3D printing is showing how it is already central to the auto industry's future.
Brands such as Stratasys create prototypes, manufacturing tools and production parts for leading automakers including Maruti Suzuki, Ashok Leyland, Honda, Mahindra and auto component maker Uno Minda, which has helped them significantly bring down time and cost involved in day-to-day operations.
The Cost of Being Prepared
Producing car components is time-consuming, resource heavy, and necessary. While new car sales make up a large percentage of auto makers' revenue pool, older cars and replacement parts represent an important source of profits. Indeed, many observers estimate the aftermarket parts sector will show healthy growth over the next few years. Moreover, auto makers must always have components for a wide range of vehicles on hand to be distributed globally.
To fulfil their obligations and provide the necessary parts for repairs, sales, and other aftermarket uses, companies must keep machines occupied that could be used elsewhere. Moreover, because parts are generally produced en masse, older parts for cars that are no longer in wide circulation can be an expensive burden that sits in warehouses.
This is a problem on several levels, starting with the cost of producing and storing parts that do not get sold. Additionally, producing these components creates material waste and takes time away from other functions. On the consumer side, this reality means that older parts or more specialized components may be rare or even non-existent, significantly raising the cost of repairs and maintenance on their vehicles.
The addition to large-scale 3D printing machines, the manufacturing floor changes the dynamics by removing many of the challenges mentioned above. Although they have become vital for rapid prototyping and design work, additive manufacturing technologies are a perfect fit for component manufacturers. Indeed, one of the biggest uses for 3D printers in today's automobile factories is in creating on-demand components that can be printed quickly and without altering production timelines.
Just-In-Time Components
Additive manufacturing offers car makers a different path with significant waste and storage need reduction. One of the biggest advantages 3D printers offer is in cutting costs due to a variety of factors. The first and most obvious is the ability to print out smaller batches of components as needed. This capacity means that automakers can cut down on their physical inventory—especially of older, less in-demand parts—and simply offer parts as needed and requested by customers. Additionally, this on-demand print capacity is not tied into other production steps.
Machines do not have to be diverted but can quickly be repurposed for a small task and then reset. The ability to create rapid prototypes adds a layer of usefulness to on-demand printing. Equipment like that lets companies quickly shift jobs to create prototypes and test new configurations of components that are more efficient. This design capability lets automakers reduce the number of components used in each part produced, lowering the need for materials and providing better results.
Similarly, the 3D process itself is significantly more efficient when it comes to waste management. Whereas traditional manufacturing creates significant waste due to the unused portions of materials simply being discarded, most 3D printing materials can be reused or recycled even in the same cycle. As such, the cost reductions alone make additive manufacturing a worthwhile investment for most companies.
Cars on Demand
Technology and our fast-paced world demand that our manufacturing keep the pace, and traditional production methods are starting to fall behind. 3D printing gives automakers the ability to keep on top of demand while still being able to innovate and provide service for customers well past the expected lifespan of an automobile. Take the case of Maruti Suzuki India. The automotive giant has leveraged 3D printing to enhance the final quality of its products by providing high quality detailing, design personalisation and seamless integration of the workflow.
Adopting additive manufacturing to improve customer service and car maintenance is not just a good idea, it's a necessary one. As 3D printing becomes more common, the auto industry will realise the real value in abandoning outdated production for fast, efficient manufacturing.
END