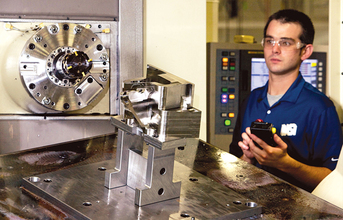
One of the misconceptions about machining titanium and similar grade materials is that general purpose machines can handle these parts just fine. The truth is, that class of machines, while ideal for many applications in a shop, have a tendency to chatter at low frequencies. This negatively affects both the quality of the part and tool life. Tooling costs can be astronomical. A machine that is designed specifically for low frequency machining dramatically reduces chatter at the necessary low RPMs that the cutting tools must run to cut these materials. Logic follows that eliminating chatter significantly increases tool life and cost savings.
Titanium 5553 is a material that exhibits superior linear-elastic behaviour. However, when machining these types of materials this behaviour dramatically increases cutting forces and generates tremendous heat directly at the cutting edge shear location. In aerospace components, tool lengths are long, axial cuts are deeper, and many application engineering hours are dedicated to process development. Unlike conventional machines that are designed for a wide range of materials, material-specific machine tools allow engineers a wider range of process opportunities in the specific cutting ranges needed. This dramatically contributes to longer tool life, chatter control, part finish quality, and predictable process control for FMS operations. Mitsui Seiki has application specific machines that have structural modifications to reduce the amplitudes of the excitation frequencies in the low frequency ranges. We have paid attention to requirements for handling the low frequency stresses such as height to width ratios on columns and tables to accommodate high moment loads, and optimal ball screw locations for axes stability. Skilled craftsmen handscrape surfaces throughout to provide the high accuracy needed to make quality parts in these materials.
Turn up the torque
To cut heavy metals, the machining system needs ample torque. The spindles should produce 2000 ft-lb (2711 N//pd//m) of torque at 100 rpm and large servo motor drives on fine-pitch lead ball screws. Ti5553 is about four times more difficult to machine than the well-established Ti6A14V in terms of tool life, stock-removal rate, and the required resiliency of the machine structure to push a cutting tool through the metal. At a depth of cut 1-1/4" diameter x 3/8" in triple nickel titanium, the tool starts to separate from the taper at about 8,500 inch-pounds of moment load on general purpose machines with a BT/Cat 50 taper.