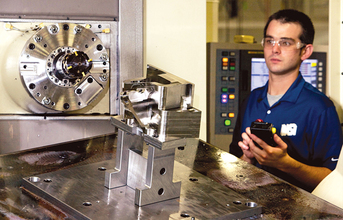
Our crystal ball shows the flurry of activity for new aircraft orders will continue for the next five years. However, even when the economic boom in the commercial aerospace sector was just a hint on the horizon, forward-looking manufacturers began seeking out the best methods for machining these demanding parts. Our company was fortunate to be involved right at the start, with Boeing's research engineers, to develop machine tool technology designed specifically to cut these hard materials. We published and presented this research as the data unfolded, and it's time for an update. Manufacturers and technology providers have learned more about the nature of the materials and what is required to turn them into parts, profitably. Further, advancements in cutting tool technology in particular have caught up with the machine tool designs, providing users with a complete, viable system that is working successfully in factories around the world.
The crux of the matter for optimum hard metal part production lies in the ability of the system to perform low frequency machining without chatter, hold tools tightly with heavy-duty tool tapers, increase machine stiffness construction, and deliver the power necessary.
Turn the frequency dial down
Machining moderately complex titanium parts up to one meter in length, which include three, four and five axes simultaneous machining, requires machine tools with the proper structural design to machine at low amplitude ranges in less than 350 Hz (especially at the 20, 90, and 320 Hz ranges). In hard metal machining, all of the materials in the machine tool structure must stay within a specific range of stiffness and resiliency so that when cutting, the spring memory of the machine is very repeatable. This repeatability is paramount for tightly controlling the cutting edge as the tools pass through the materials. A one-inch diameter, four-flute end mill, for example would be run at about 90 RPM. Each time a cutting edge engages with the material, it sends a shock wave into the machine. As each cutting edge ‘hits' the metal in a consistent, repetitive sequence it creates a low frequency wave into the machine.