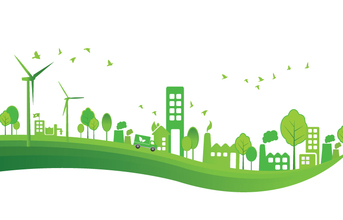
Reuse & recycling
Recycle and reusing are essential parts of sustainable processes. Marching its way in this direction, Racold Thermo treats waste water generated in the paint shop so that it can be utilised for gardening purpose. Similarly, Marolia clarified that at Godrej & Boyce's Vikhroli and Shirwal, 100 percent of the water requirement in the powder coating pre-treatment process is fulfilled by recycled water, which is made process ready through the use of reverse osmosis (RO) treatment.
On the other hand, Henkel Adhesives Technologies' Thane plant took an initiative to recycle raw material drums for packaging of finished goods with all quality controls in place; thereby, reducing 64,800 Kgs of waste generation per annum. "While, our Turbhe plant saves 14,60,000 litres of water each year by distillation of a water-glycol mixture and reusing it in the cooling towers as make up water," emphasised Bandyopadhyay.
HIL reuses the water discharge from the RO for toilet flush. "That's not it. Following the mantra of recycling, we also recycle our products 100 percent after they complete its lifetime," Mati revealed.
Elaborating on the efforts made by Dalmia Bharat in the area of recycling, Tripathy said, "We continue our commitment to promote the industrial ecology through use of various industrial wastes (alternative raw material) such as fly ash (waste from coal based thermal power plants), blast furnace slag (waste from steel industry), chemical gypsum, red mud (waste from aluminium industry), etc. Our alternative raw material input for the company was about 28.5 percent in FY 2014-15. Further, we have registered carbon footprint of less than 500 kg CO2/ton of cement (FY 2015-16). Our eastern operations produce 100 percent blended cements with associated carbon footprint of less than 370 kg/ton."
Reusing and recycling are the key areas where Henkel Adhesives Technologies is working on to achieve its sustainability vision. The company focuses on three areas; i.e., water, energy (power and fuel) and waste across manufacturing sites in the country. To attain reduction, the company works on the three identified areas under the categories of ‘Reduce', ‘Reuse' and ‘Recycle'. "With this regard we have Sustainability Vision 2020, considering 2010 as the baseline year. This vision includes to reduce consumption of resources by 30 percent; to reduce carbon footprint from logistics operations by 25000MT of CO2e or 6 percent and to ensure 40 percent of Henkel's manufacturing sites across the globe comply with zero waste to landfill strategy," elaborated Bandyopadhyay.
However, in order to achieve these targets, there is a necessity of having a robust monitoring system. "To meet these targets, achievement against each set of parameters is measured, reported and monitored on a month-on-month basis," he added.
Constant monitoring is a key
Seconding the same, Tripathy said, "Performance measurement is the first step to the effective management and sustainable production. Realising the need of effective performance measurement, we have developed monthly dashboard for carbon footprint estimation. On monthly basis, an internal carbon footprint based benchmarking is carried out for our manufacturing plants spread across India."
(Continued on next page)