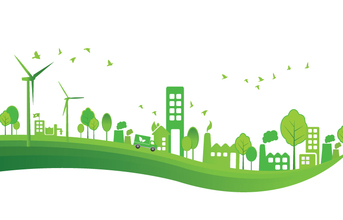
As Winston Churchill once said, "To improve is to change, to be perfect is to change often", the companies need to be perfect in what they produce as well as how they produce it. In today's era, the focus on reducing impact on the environment is immense and that has direct effect on the business efficiency. Speaking on the same, Bappa Bandyopadhyay, Director - Operations & Projects, Henkel Adhesives Technologies India Pvt Ltd said, "We are convinced that sustainability and reduced environment footprint is becoming increasingly important for business success, supporting growth, improving cost efficiency and reducing risks."
Additionally, maintaining and creating a strong brand image in the society is also one of the essential aspect that is directly related to ‘being green'. Even customers are being selective about suppliers not only on the basis of the quality of the product but also on suppliers' efforts of being soft on the environment. "The drive to reduce resource consumption and improve efficiency directly translates into business profit," noted Zurvan Marolia, Sr Vice President and Head - Product Supply, Godrej & Boyce. Hence, companies are setting goals towards being green.
Translating its thoughts about being eco-friendly into action, HIL launched UPVC and CPVC pipes and fittings couple of years back, under the brand Aerocon. Speaking on the same, Lokanath Mati, Operations Head, AAP Business, HIL stated, "We understand the importance and the need to employ green technology and developing green products, as that is where the future lies. As a result we take all necessary steps to ensure that our manufacturing process and products are eco-friendly. For example, as norm of the company, we do utilise 100 percent heavy metal free raw materials and we are the first company in the country to do so in our category."
Cement is another industry that is considered to be one of the most hazardous to the environment. However, Dalmia Bharat, an Indian cement producer, is taking steps to make its processes friendly to the nature. "With cement to clinker ratio of about 1:7, today we are one of the most efficient cement producers globally. Through in-house research and development, we have strengthened our competitiveness in terms of operational efficiencies leading to greater returns, cost reduction and intrinsic stakeholder value," asserted Prashant Tripathy, Group Head - Manufacturing, Dalmia Cement Bharat Ltd (DCBL).
Alternatively, Godrej & Boyce's most of the plants have implemented green manufacturing processes and hence have earned GREENCO certifications. "Our pioneering efforts in manufacturing processes include focus on improving energy efficiency, increasing the component of renewable energy, reducing fresh water footprint, chemical management and the management of hazardous & non-hazardous waste. On the water front, at the Vikhroli establishment, all of our plants are connected to a central Effluent Treatment Plant (ETP) and Sewage Treatment Plant (STP). Most of our upcountry manufacturing locations are equipped with in-house ETP and STP ensuring zero liquid discharge to the environment. This provides the opportunity to treat and use recycled waste water for its processes. Most plants also have rain water harvesting facility. We are consciously working towards increasing its renewable share through use of solar roof top panels, biomass energy through gasifier, thermic fluid heater at plants, and strategic power purchase agreements," Marolia informed.
(Continued on next page)