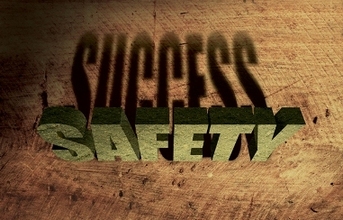
We often make the mistake of thinking that a ‘slow' leak is a ‘small' leak. A slow leak results in a large spill if the detection system is too insensitive to detect leaks below a given threshold or below a certain percentage of flow. Far too many leaks are discovered when someone notices the smell of fuel, or after surface/below ground water has become contaminated. The key components of an effective fuel detection system include sensing cables, probes and sensor interface modules and alarm panels.
Sensing cables provide early detection of below ground or above ground ‘weeps and seeps' before they accumulate into large spills. And the location is reported to the nearest meter. Probes detect fuel floating on water or fuel accumulating in low spots like sumps or valve pits or on flat surfaces like pump pads. The probes react instantly to even a thin film of fuel and can be reset and reused and even ‘wet tested' if desired. The sensor interface modules and alarm panels are designed to energise the sensor cables and probes, monitor their condition and report the existence and location of any leak detection to operators and other alarm and supervisor systems.
High-integrity pressure protection system
This is a safety instrument system (SIS) designed to prevent over-pressurisation of any line or unit at a chemical plant or oil refinery. In old traditional systems, over-pressure used to be dealt with through relief systems. Once a set pressure is exceeded, a relief system opens an alternative outlet for the fluids in the system. This is done to avoid further build-up of pressure in the protected system. This alternative outlet generally leads to a flare or venting system to safely dispose the excess fluids. In sharp contrast to a relief system, this system aims at stopping the inflow of excess fluids and containing them in the system.