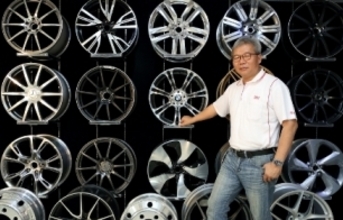
OLP40 probes allow SAI to carry out in-process measurement control to achieve tolerance of less than .0.02 mm, and can replace human measurements and updates to workpiece coordinates. This greatly improves cutting and efficiency for surface precision processing after coating.
Even more importantly, it reduces rework by 80 percent, as before the introduction of in-line measurement systems wheel production generally had to be processed twice to achieve the necessary precision. When combined with Renishaw software, the probes not only play a role in guidance during production, but also provide in-process control and real-time feedback, immediately updating and correcting data during metal cutting, and efficiently monitoring and controlling dimensions and deformations.
Renishaw machine tool probe systems have allowed SAI to increase production precision and product quality, while also reducing scrap from 2-3 percent to 0 percent, and improving production efficiency.
Precision processing for car chassis
The automotive industry has already evolved from focusing on basic safety requirements and performance towards enhanced driving comfort, improved fuel efficiency and reduced emissions. The safety and stability of lighter vehicles moving at high speed is closely connected to the manufacturing of the car chassis.
The higher the precision of chassis produced with aluminium alloys, the safer and more stable the car is when travelling at speeds as high as 200 km/h, and the more comfortable the driving experience. The lighter the chassis, the lower the fuel consumption, and thus the easier it is for the vehicle to meet environmental requirements.
SAI has continually improved its forging and mechanical processing technology. The company moved into the processing and production of precision car chassis in 2011. SAI now has 38 Tongtai high end five-axis CNC machine tools, all of which are equipped with Renishaw OMP60 optical machine tool probes and NC4 non-contact laser tool setters.
Unlike wheel rim production, chassis production tends to involve high volume and lower diversity, but nevertheless still requires high-precision metal cutting and processing. Renishaw OMP60 optical machine tool touch probes use advanced modulated optical transmission to provide 360° signal transmission. The probe simplifies measurement and calibration processes, thereby achieving high-precision measurement for workpieces with complex profiles.
The NC4 uses innovative laser technology to perform high-speed, high-precision measurement of cutting tools as small as 0.2 mm, and to perform tool breakage detection on cutting tools as small as 0.1 mm. Its non-contact method avoids the potential for causing wear or damage of cutting tools.
(Continued on the next page)