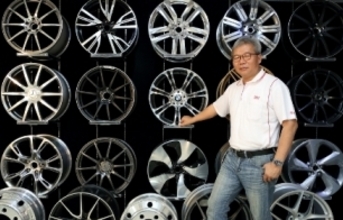
SAI is currently focused on supplying high-quality forged metal products. SAI's customers are all high-end automobile manufacturers that demand specialised technologies and services, including some of the world's top-tier car makers such as BMW, Mercedes-Benz, VW, Porsche, Ferrari, Ducati, Bentley, Audi, Rolls Royce, Jaguar, Land Rover, Ford, Chrysler, Toyota, GM and Honda.
The production of aluminium forged wheel rims
The forged wheel production process is complex, particularly for low-volume, high-diversity production. SAI produces more than 200 types of wheel which requires the utmost production flexibility.
Strict standards are applied to workpiece setting, reference measurements and key dimension detection during metal processing, as the precision requirements for machining wheel mounting surfaces exceed the requirements of even the aerospace industry.
SAI currently has 600 CNC machine tools working on wheel rim production, including 150 Victor Taichung lathes and 450 YCM milling machines. All these machine tools are engaged in production on a three shift process five days per week. So how does SAI ensure that the precision and stability of 600 machine tools remains consistent?
In order to increase production precision and reduce scrap, SAI equipped the relevant lathes with Renishaw OLP40 touch probes, which use optical signal transmission and are adapted for turning processes. The CNC milling machines were equipped with RMP60 machine tool probes which use wireless radio transmission to measure workpiece position and reference height, as well as providing in-line key dimension detection, thereby increasing production performance.
Y.C.Kao, Senior Manager of SAI's Wheel Production Department, explains: "The automated workpiece setup enabled by Renishaw machine tool probes allows us to ensure that the cutting dimensions remain stable and consistent when we are producing wheel rims, as well as effectively reducing human error. For example, the air valve hole cutting thickness Process Capability Index (CPK) rose from 0.71-1.13 to 1.35-1.43 when using Renishaw machine tool probes."
3D appearance modelling for forged wheel
Wheel styling design has moved from flatter surfaces towards more 3D effects in recent years, causing wheel rims to become ever larger, and placing increasingly stringent demands on processing precision. Until 2011, SAI's acceptable tolerances for wheel rim production (with the flatter designs used at the time) were 0.05-0.10mm.
However, the tighter tolerance requirements of the current 3D designs has gradually increased cutting times and processing; wheel rim appearance processing takes as long as 180 to 240 minutes, with the result that any rework imposes considerable pressures in terms of both production time and cost.
(Continued on the next page)