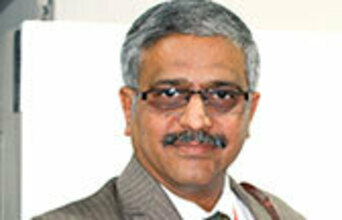
The global machine tools industry is set to grow into a $73.5 billion market by 2027. How can India be an effective contributor to this market?
This is a question that's been topmost & foremost and also plaguing and troubling, companies as well as the industry association. I believe that the scope is huge. Currently, the Indian manufactured machine tools are not even 1 per cent of the global consumption, and post-COVID, Eurasia war, etc. shift is expected. The initial part of globalisation was to make somewhere sell everywhere, think global act local, etc. Now, it is going to be the era of regionalisation of markets and manufacturing. Currently, there is a lot of need for an interaction to happen between components and the machine tool manufacturers and some realignment through the industry. We have the language, education, people, judiciary, intellectual property, etc., giving India a fair chance of growing in the global market. In the coming 5-10 years, I believe we will see a good CAGR of 10 to 12 per cent growth and contribution from the machine tool sector.
How much has Aatmanirbhar Bharat helped the machine tools sector? How is Ace Micromatic contributing to the movement?
At this point in time, looking at all the IPPs and the incentives that the government is giving, there's nothing that directly benefits the machine tool or the cutting tool sector. Although the automotive industry (which drives the machine tools sector) being included in Aatmanirbhar Bharat has certainly helped. There's also a huge thrust on exports that the government is looking at to make in India for the world where the machine tools or capital equipment/capital sector is focused on. So, at this point, the support is indirect. What the government should really do, which they are doing, but not fast enough, is strongly focus on infrastructure and ease of exporting. While the Indian market is fairly okay with delivery time in weeks, and project institutional funding to buy machine tools, the global market works on sales from stocks and more creative market funding for machines. Hence, the government needs to look at offering single window clearances, better ports, cheaper funding, etc., to enhance India's focus on Aatmanirbhar Bharat for machine tools. We are probably the only machine tool company that has been looking at exports for the last 15-18 years in a very focused manner. I am also happy to mention that while our top line is growing, our percentage of export has also been steadily growing. Currently, nearly 9 per cent of our turnover comes from exports. We are now targeting to reach a 15 per cent mark in the next 3-5 years.
As you said, the automotive sector is one of the biggest contributors to the machine tools sector. Given the trend of rapid electrification of vehicles and reducing ICE vehicles, how is it going to affect your industry? Further, how are you preparing to be a part of the EV market?
The electrification of vehicles will certainly have an effect on the machine tools sector, and there is no question about it. There's enough research that's done, where from the sheer number of transmission parts, the engine parts that are required - the prime mover - are completely gone from an ICE to EV. Currently, nearly 50-53 per cent of the parts in an ICE vehicle comes from the metal cast, which is machined and made. So, this is the hard part. However, over the last five years, if you take the Indian machine tools industry as a whole, the percentage of dependence on machine tools for the automotive industry in the 80s was over 85-90 per cent. Today, the dependence has come down to less than 60 per cent. So, there has already been a conscious shift from the automotive industry. Further, while EVs are going to grow, there are several other infrastructures that are set to grow, which are far more in number compared to cars. Additionally, the aerospace and defence sectors will continue to need high-accuracy machined parts. So, it is important to analyse how the companies look at it and start the diversification. While fundamentally the machine does not change, it is more about precise and reliable performance, measurements, and how to use it and get a better output while using different materials.
Ace Micromatic, not too long ago, introduced a metal 3D Printing system - STLR-400. Can you elaborate on the product? What sets it apart from other metal 3D printers in the market?
The AMACE STLR 400 is a large format, high productivity, industrial grade metal 3D printer, which employs the most advanced and technologically mature process in metal 3D printing, called Laser Powder Bed Fusion (L- PBF). It is designed and developed to suit serial production applications, allowing for multiple parts to be nested within it or for larger-sized parts to be printed. The team at AMACE, through rigorous R&D over the years, have proved out multiple materials like stainless steels, aluminium alloys, tool steels, Inconel, titanium alloys and many more. What we believe sets it apart is its innovative, multi-blade recoating system designed to enhance the productivity of printing, especially during production-related activities. Further, its smart power management system, an in-situ inspection of part dimensions, automatic filtration system, user-friendly digital cockpit format for data display on the Graphical User Interface (GUI) and the remote monitoring & control of the machine are some of the many features that make the machine a smart one and most suited for a production environment.
With the growing digitalisation and competition, how can India become a global hub for manufacturing? In what ways can the government help the sector?
India has in its own way made some presence in global manufacturing in the automotive, especially in the two-wheeler & small passenger car segments. To become a global manufacturing hub, scale and agility are two key requirements. In phase one, we will need to augment skills competencies in manufacturing & make investments for infrastructure in logistics & supply chain. The government should lead the way along with the private enterprise with committed investments which will enable the flow of technology. The next phase will be about scaling and optimisation.
The global machine tools industry is set to grow into a $73.5 billion market by 2027. How can India be an effective contributor to this market?
This is a question that's been topmost & foremost and also plaguing and troubling, companies as well as the industry association. I believe that the scope is huge. Currently, the Indian manufactured machine tools are not even 1 per cent of the global consumption, and post-COVID, Eurasia war, etc. shift is expected. The initial part of globalisation was to make somewhere sell everywhere, think global act local, etc. Now, it is going to be the era of regionalisation of markets and manufacturing. Currently, there is a lot of need for an interaction to happen between components and the machine tool manufacturers and some realignment through the industry. We have the language, education, people, judiciary, intellectual property, etc., giving India a fair chance of growing in the global market. In the coming 5-10 years, I believe we will see a good CAGR of 10 to 12 per cent growth and contribution from the machine tool sector.
How much has Aatmanirbhar Bharat helped the machine tools sector? How is Ace Micromatic contributing to the movement?
At this point in time, looking at all the IPPs and the incentives that the government is giving, there's nothing that directly benefits the machine tool or the cutting tool sector. Although the automotive industry (which drives the machine tools sector) being included in Aatmanirbhar Bharat has certainly helped. There's also a huge thrust on exports that the government is looking at to make in India for the world where the machine tools or capital equipment/capital sector is focused on. So, at this point, the support is indirect. What the government should really do, which they are doing, but not fast enough, is strongly focus on infrastructure and ease of exporting. While the Indian market is fairly okay with delivery time in weeks, and project institutional funding to buy machine tools, the global market works on sales from stocks and more creative market funding for machines. Hence, the government needs to look at offering single window clearances, better ports, cheaper funding, etc., to enhance India's focus on Aatmanirbhar Bharat for machine tools. We are probably the only machine tool company that has been looking at exports for the last 15-18 years in a very focused manner. I am also happy to mention that while our top line is growing, our percentage of export has also been steadily growing. Currently, nearly 9 per cent of our turnover comes from exports. We are now targeting to reach a 15 per cent mark in the next 3-5 years.
As you said, the automotive sector is one of the biggest contributors to the machine tools sector. Given the trend of rapid electrification of vehicles and reducing ICE vehicles, how is it going to affect your industry? Further, how are you preparing to be a part of the EV market?
The electrification of vehicles will certainly have an effect on the machine tools sector, and there is no question about it. There's enough research that's done, where from the sheer number of transmission parts, the engine parts that are required - the prime mover - are completely gone from an ICE to EV. Currently, nearly 50-53 per cent of the parts in an ICE vehicle comes from the metal cast, which is machined and made. So, this is the hard part. However, over the last five years, if you take the Indian machine tools industry as a whole, the percentage of dependence on machine tools for the automotive industry in the 80s was over 85-90 per cent. Today, the dependence has come down to less than 60 per cent. So, there has already been a conscious shift from the automotive industry. Further, while EVs are going to grow, there are several other infrastructures that are set to grow, which are far more in number compared to cars. Additionally, the aerospace and defence sectors will continue to need high-accuracy machined parts. So, it is important to analyse how the companies look at it and start the diversification. While fundamentally the machine does not change, it is more about precise and reliable performance, measurements, and how to use it and get a better output while using different materials.
Ace Micromatic, not too long ago, introduced a metal 3D Printing system - STLR-400. Can you elaborate on the product? What sets it apart from other metal 3D printers in the market?
The AMACE STLR 400 is a large format, high productivity, industrial grade metal 3D printer, which employs the most advanced and technologically mature process in metal 3D printing, called Laser Powder Bed Fusion (L- PBF). It is designed and developed to suit serial production applications, allowing for multiple parts to be nested within it or for larger-sized parts to be printed. The team at AMACE, through rigorous R&D over the years, have proved out multiple materials like stainless steels, aluminium alloys, tool steels, Inconel, titanium alloys and many more. What we believe sets it apart is its innovative, multi-blade recoating system designed to enhance the productivity of printing, especially during production-related activities. Further, its smart power management system, an in-situ inspection of part dimensions, automatic filtration system, user-friendly digital cockpit format for data display on the Graphical User Interface (GUI) and the remote monitoring & control of the machine are some of the many features that make the machine a smart one and most suited for a production environment.
With the growing digitalisation and competition, how can India become a global hub for manufacturing? In what ways can the government help the sector?
India has in its own way made some presence in global manufacturing in the automotive, especially in the two-wheeler & small passenger car segments. To become a global manufacturing hub, scale and agility are two key requirements. In phase one, we will need to augment skills competencies in manufacturing & make investments for infrastructure in logistics & supply chain. The government should lead the way along with the private enterprise with committed investments which will enable the flow of technology. The next phase will be about scaling and optimisation.