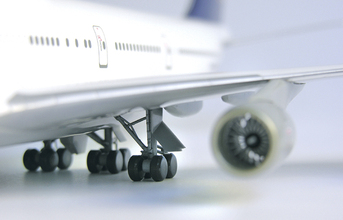
Light-weighting is a key objective for all aircraft manufacturers. Making a plane lighter reduces fuel use, lowering operator costs and the negative impact of flying on the environment. This is where composites are finding its place!
Fuel is the number one expense for airlines, so it's no surprise that they are continually looking for ways to lighten the load. A figure brought to the forefront by Norwegian economist Bharat P Bhatta's proposed pay-as-you-weigh pricing model for passenger fares, is his estimate that a reduction of one kilogram of weight could result in a fuel saving of 3,000 US dollars per year.
All of these measures add up to lower operator costs, less fuel and a reduction in CO2 emissions. As effective as these in-cabin changes may be, potentially greater savings can be made in the fundamental design of the plane. One option for this is a shift from metal components to composites.
Composite bearings
Trelleborg Sealing Solutions has a focus on composites at its facility in Albany New York in U.S. as well as in Rotherham, England, where the unique Orkot® material is manufactured.
"Traditionally, Orkot® has been used in bearings for ships and hydropower plants," says Brian Bowen, who is heading up a project to transfer this proven technology to aerospace applications. "Metal bearings feature in the landing gear shock absorbers of planes and if these can be successfully replaced with composite bearings instead, a huge potential saving can be made by operators through light-weighting."
Not just lighter in weight replacing a steel/ bronze bearing with a composite bearing saves weight due to the specific density of the materials used. The specific density of steel is eight grams per centimeter cubed and bronze is 8.75. Polymer bearings have a specific density of just 1.25 grams per centimeter cubed; a typical saving of 7.5 in volume per unit.
"Composite bearings have other advantages too," continues Brian. "Friction is low, running dry or lubricated, and constant. There's no surface coating to wear off, and when running dry, there's no maintenance.
"The composite bearings are easier to fit than metal ones and their flexible base material spreads load more effectively, allowing a larger contact area. They also have no edge loading, are impact resistant and oversized repair parts require no tooling. All in all, the composite bearing is a promising alternative to metal ones."
Eliminating metallic wear particles
A less obvious but important additional benefit of composite bearings, that has been identified by Trelleborg Sealing Solutions, is the exclusion of metallic particles from the hydraulic system.
Brian explains: "We've observed that customers who use metallic bearing shells have an increased risk of metallic wear particles in the shock absorber hydraulic fluid. Over time these metallic wear particles can scratch the counter surfaces of the shock absorber slider, and more critically, can damage the soft polymer seals. If the dynamic seal caps become scratched, then this can lead to a reduction in the service life of the shock absorber. Composite bearings do not generate such abrasive wear particles, extending the life of seals and the system itself."
However, despite all these benefits, the biggest advantage of the composite bearing remains its lighter weight. To prove this Trelleborg Sealing Solutions undertook tests to verify the potential weight saving from switching from metal to composite bearings.
Huge savings per year
"The total saving from just the replacement of the bearings in the landing gear shock absorbers is 20 kilograms per plane. If we go back to Bharat P Bhatta's estimated fuel saving of 3,000 US dollars per year per kilo that equates to 60,000 US dollars per year per plane.
"And the shock absorber bearings are not the only application we're looking at for Orkot®. There are also the LG pin bearings, landing gear actuation bushings, door hinges and cargo handling rollers and wear pads," concludes Brian.
For more info, contact:
Trelleborg India Pvt Ltd
tssindia@trelleborg.com