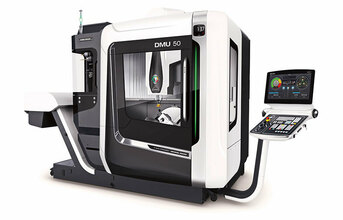
The DMU 50 3rd Generation achieves a unique degree of precision of less than 6 μm that is unbeatable in this segment thanks to its one-piece machine bed on the one hand and on the other its innovative cooling of the guides, drives and table bearings. Directly driven ball screws and direct path measuring systems in all five axes round off the equipment with regard to the machine's high degree of precision. The DMU 50 3rd Generation can be expanded with coolant tanks and tool measurement as an option.
A 21.5" ERGOline® with CELOS® and Siemens 840D solutionline as well as a 19" ERGOline® with HEIDENHAIN TNC 640 are available as modern control options. DMG MORI also has diverse automation solutions in its program for the DMU 50 3rd Generation, such as workpiece or pallet handling systems. This enables the world premiere to master challenging applications in the future-oriented aerospace, medical, automotive and energy branches - a demand that was already taken into account during the practice-oriented development of the machine. In other words, the DMU 50 3rd Generation continues to fulfil all the requirements that ensure it will remain DMG MORI's bestselling 5-axis model.
Highlights DMU 50 3rd Generation
• 78% larger work area
• 40% higher rapid traverse speeds 42 m/min as standard
• 28% greater swivel range, Swivel rotary table with -35° / +110°
• Experience gained from morse than 10,000 machines already supplied
• 5-axis simultaneous machining as standard
• 36 months warranty for all master spindles with unlimited spindle hours for all new machines in 2018
END