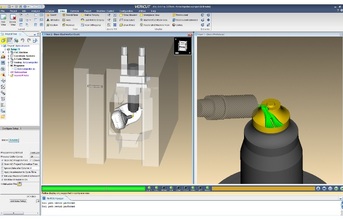
According to the Association for Manufacturing Technology, 5-axis mills and mill/turn machines have increasingly become popular, for a good reason. They enable the manufacturer to drastically reduce machining time and the number of set-ups required to complete a job. Simulation software takes the fear out of programming a multi-axis machine. When an NC program can be simulated, from the same code that will be sent to the machine, there is no excuse for not taking full advantage of a 5-axis machine's capabilities.
Machining before machine arrival
Even today, with ups and downs in machine tool sales, there is still considerable time between the date when the machine is ordered, and the date that it is installed and ready to cut the parts. With simulation software, the manufacturer can be ready to create parts on the first day the machine is installed.
CGTech has partnerships with many of the leading machine tool companies and they will often supply the CAD geometry for its joint customer's machines - before the machine is even shipped. The manufacturer can then be proving out programs right away. Some of the customers can discover the efficiency and suitability of the machine configuration ordered even before the machine is delivered. By catching the machine specification mistake early, the customer can change the order before the machine is delivered.
Opting for the right machine using virtual simulation
The aerospace manufacturer working on the leading edge took the idea a step further. After proving the 5-axis milling process could work, they were ready to order production machines. Rather than simply picking the machine from a catalog, they designed the machine in their simulation software, where they had already proven the process would work. These files were then sent to the machine tool builder who built the machine exactly to their specifications as described in a virtual machining simulation.
Another leading aerospace company created programs for more than 200 parts and proved them using virtual simulation software even before the arrival of machines on their shop floor. All the machines ordered were built using virtual simulation software and all NC programs were proved on a virtual machine. The machine loading plan was also prepared, thanks to accurate cycle times provided by simulation software. Once the machines arrived, they cut the parts without any further delay.
Summary
By maximizing the use of simulation software, shop floors don't need to wait for NC programs. There are always opportunities to improve an existing process, and simulation software can help by giving the NC programmer the freedom to try practically any machining technique in a virtual world. Only creativity and a good virtual platform are required to accomplish the job!