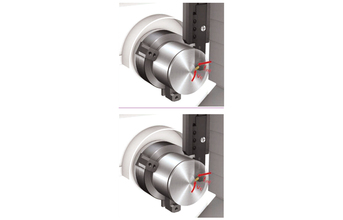
The y-axis parting principle
The principle behind Y-axis parting is incredulously simple. While conventional parting off tools align with the X-axis of the machine tool, the Y-axis tool has simply been rotated 90° anti-clockwise to align with the Y-axis. In a conventional tool configuration, the relatively long and slender parting blade and holder is fed at a 90° angle into the rotating workpiece. The largest cutting force is generated by the cutting speed and the rest by feed motion. The consequence is a resultant force vector that is directed diagonally into the tool at an angle of roughly 30°, in other words across
a very weak section of the blade. To avoid tool breakage, this is compensated by reducing the blade overhang and by increasing the blade height, which in turn sometimes compromises the usability of the tool. By turning the tip seat 90 degrees and utilizing the Y-axis, the tool can cut its way into the workpiece essentially with its front end, which nearly aligns the resulting cutting force vector with the longitudinal axis of the blade. FEM analyses performed by the Sandvik Coromant R&D team confirmed that the new solution eliminates critical stresses and increases the blade stiffness by more than six times compared to conventional blade design.
To put it short; when switching to parting in the Y-axis plane you get a beneficial direction of the cutting force resulting in less instability and vibration. This means you can ramp up feed rate without losing stability or breaking the tool for an extremely secure and productive parting process. Simple as that.
For more info about y-axis parting with
CoroCut QD, visit
www.sandvik.coromant.com/corocutqd
END