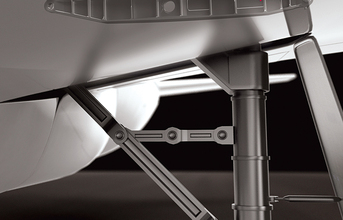
The following overviews show example machining rates and tool life, which could be implemented when machining pockets on a generic component:
1. M3255 tangential porcupine milling cutter / D = 50, z = 5 / WSM45X:
Roughing - Pocket: 274 x 120 x 74 mm: vc = 40 m/min, fz= 0.15 mm, ap= 37.0 mm (2 steps), ae= 30.0 mm (concentric tool path)
The result: Machining volume: 212 cm³/min, tool life: 70 mins (t/pocket: 14 mins)
2. Ti50 ConeFit Prototyp / D = 25, z = 5 / solid carbide changeable head:
Semi-finishing and finishing - Pocket: 274 x 120 x 74 mm:
vc= 90 m/min, fz= 0.1 mm, ap= 16.0-22.0 mm (variable), ae= 3.7 mm (semi-finishing), 0.3 mm (finishing) The result: Machining volume: 33 cm³/min, tool life: 60 mins (t/pocket: 14 mins)
3. M4002 high-feed face milling cutter / D = 50, z = 5 / WSM45X:
Roughing - Pocket: 254 x 127 x 42 mm: vc= 60 m/min, fz= 0.7 mm, ap= 1.5 mm, ae= 50 mm
The result: Machining volume: 93 cm³/min, tool life: 40 mins (t/pocket: 10 mins)
Milling with a difference: High dynamic cutting
A very good example of an intelligent machining strategy is "high dynamic cutting" (HDC). This improves both costefficiency and process reliability. With high dynamic cutting, the machining conditions remain constant - along, therefore, with the forces applied to the tool cutting edges and the process temperature. The corresponding functions are provided by modern CAM software. Advantages: Better performance and greater process reliability. The constant engagement condition generates lower vibration - and thus results in a higher tool life at a lower tool wear rate. The Walter Prototyp Ti40 solid carbide milling cutter is perfectly suited to this machining strategy.
4. Ti40 Prototyp / D = 20, z = 5 / solid carbide end milling cutter for titanium materials:
High dynamic cutting, triangular pocket: 200 x 92 x 48 mm: vc= 115 m/min, fz= 0.134 mm, ap= 47.5 mm, ae= 2 mm
The result: Machining volume 139 cm³/min (t/pocket: 9
mins).
Source: Walter Tools India
END