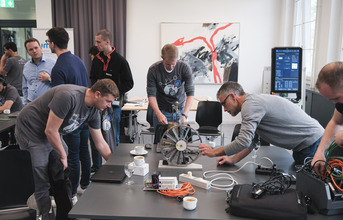
Experts from the machinery and plant engineering sectors met for the second time for a umati hackathon. The aim of the umati initiative is to further advance connectivity and digitalisation in machine tools. The focus of this year's hackathon was on expanding the connectivity of older generations of existing machines using umati. The experts met at the cylindrical grinding machine specialist, Fritz Studer AG, a company of the UNITED GRINDING Group.
A umati hackathon is when around thirty digitalisation experts from the machine and plant engineering sectors of different industries meet and network machines together, implement standardised data models, and generate and test code for two days. After 2022, it is the second such event, this year, it took place in May in Steffisburg, Switzerland, at Fritz Studer AG, the cylindrical grinding machine specialist of the UNITED GRINDING Group.
"As the host of this event, we enable a creative platform that brings developers from different companies together - not for their own purpose, but always with a focus on specific customer benefits," says Christian Josi, Head of Digital Engineering at the UNITED GRINDING Group. We are big proponents of umati and have supported the initiative since day one.
umati stands for "Universal Machine Technology Interface" and aims to introduce a universal manufacturer-independent data interface for machines based on OPC UA. Thanks to this interface, machines on the shop floor can communicate with each other and with their production environment in a uniform language.
The VDW and VDMA are the initiators and sponsers of this initiative. "Standardisation of communication and interfaces is enormously important for machine tools and the industry of the future," says Alexander Broos, Head of Research and Technology at VDW and project manager, umati.
This uniform language can only be developed in cooperation with the various machine manufacturers. Around 310 partners from all over the world are now involved in umati. All of them share the goal of making their customers' work lives easier and increasing productivity in production by harnessing the potential of digitalisation. This is achieved with umati through the implementation of the OPC UA communication and interface standard, which can now be used for a wide range of machine tool applications through numerous sub-specifications, so-called companion specifications. -The advantages are:
- Quick overview of all machine, process, and production data, as all machines can be connected to a monitoring system, which makes it significantly easier to uncover optimisation potential in production
- Plug and Produce - i.e., the simple connection of machines from different manufacturers to one another and to the superordinate production system without any time-consuming coordination and tedious manual configuration ahead of time, which saves a lot of time and resources
- The variety of different interfaces is reduced with umati; this improves transparency and manages the complexity
The focus of the most recent hackathon was on the integration of existing machine tools using the OPC 40501 "UA for Machine Tools". While new machines are predominantly equipped with the integrated umati standard today, there is great potential in existing machines, known as "brownfields." The importance of "Brownfield" is so significant, because machines in general, and machine tools in particular have a long service life, and several machines of different years of manufacture, can often be found in one production. At the hackathon, the experts impressively demonstrated that umati is also suitable for existing machines - regardless of the year of manufacture and the brand.
Another showcase from the Hackathon in Steffisburg was the implementation of the first standardised energy consumption data of the "Energy Monitoring" expansion of the OPC 40001 "UA for Machinery," which is currently under development. Electrically and pneumatically operated consumers provided their values in a uniform language on the data interface. This further development is an example of how umati does not stand still, but makes advancements and adapts to constantly changing customer needs.
Christoph Plüss, CTO of the UNITED GRINDING Group, shared, "umati has succeeded in combining the expertise of manufacturers in an initiative that may even be competitors in day-to-day business to pursue a common goal: to drive forward digitalisation and thus offer the customer added value. Only by joining forces can an industry standard be created and developed, and I am convinced that this is the right path and that our customers will also benefit from it."