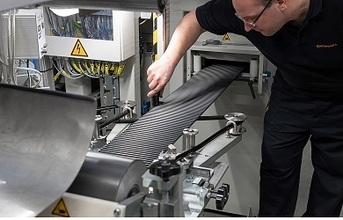
Galvanized steel cords are integrated into the belt’s interior and coated with polyurethane, which furnishes both the teeth and the back of the belt and forms an outstanding connection with the tension member. Polyurethane is particularly abrasion-resistant.
Technology company Continental is equipping the wind turbines made by Chinese manufacturer Xinjiang Goldwind Science and Technology with drive belts. In the unique and patented construction, the belts manufactured at the Dannenberg location in Germany allow the rotor blades to be adjusted at any time without the aid of gears or hydraulics. Continental engineers used an optimal combination of two tried-and-tested timing belt technologies to develop the belts. Back in 2018, Continental invested around €2 million in a new facility at the site in Lower Saxony to meet the Chinese company's annual demand for over 100 kilometers of drive belts.
Goldwind is one of the few providers on the market to use a drive without a gearbox to adjust the blades, which is becoming vital to be able to respond flexibly to changing wind strengths. "Goldwind relies on timing belts," says Rolf Marwede, who heads Continental's location in Dannenberg. "There are some advantages to this. For instance, the system is less complex and therefore less prone to vibrations and disturbances at the top of the nacelle. Our belts are also extremely low-wear and durable."
The belts provided by Continental do not require any oil for lubrication and are very low maintenance overall and also largely corrosion-resistant. In offshore wind turbines in particular, this last point presents a major advantage over conventional metal designs that are permanently exposed to salty sea air. "In comparison with gearbox solutions, a simpler design that uses drive belts is also more cost-effective and more efficient in the long term," says Marwede. If there is a defect, the system can also be repaired very quickly because only the belt needs to be replaced, not the whole gearbox.
For Goldwind, it was important to develop a low-maintenance and simpler alternative to the conventional gearbox system. The chosen belt solution was an exact match for these requirements and is based on Continental's Synchrodrive technology. Galvanized steel cords are integrated into the belt's interior and coated with polyurethane, which furnishes both the teeth and the back of the belt and forms an outstanding connection with the tension member. Polyurethane is particularly abrasion-resistant.
The two opposing impact directions of the steel cords and their strands result in neutral running properties, making the belts extremely resilient. It is not uncommon for there to be around 12 million reverse bending cycles. But what makes the belts used by Goldwind so unique is the special fabric, which is manufactured at Continental's location in Northeim. The specialist in drive belts is making use of its Synchrochain technology expertise for this application. "The fabric reduces wear and absorbs noise and also provides a much more stable structure for the timing belt. This enables us to significantly improve the belt's performance yet further," explains Marwede. The fabric reinforces the teeth and improves run-in behavior, which in turn boosts efficiency. "Ultimately, we have brought together two product groups to develop the ideal solution for Goldwind's application."
Continental manufactures the belts for Goldwind at its Dannenberg site, which is a competence center for the production of polyurethane belts within the company. The technology company installed a new facility for this very purpose last year. The hall out of which the facility operates, which was newly built in 2017, offers space for further production expansion. "At a single location, we can not only offer Synchrodrive and Synchrochain belts, but also combine both product types with each other - just like in Goldwind's application has never been done before and makes us a much more effective partner," sums up Marwede.
Continental therefore sees its partnership with Goldwind as an important cornerstone on which to further develop its focus on the topics of sustainability and resource conservation. In addition to drive belts, the company supplies the wind turbine manufacturer with mounting elements, films for reducing wind resistance, and hydraulic lines. Wind is an unlimited resource. Wind turbines are considered clean, with the wind power they provide being the ideal complement to other energy sources. By the end of 2019, wind turbines with a total output of around 650 gigawatts had been installed around the world. By way of comparison, 40 gigawatts would be enough to supply electricity to every household in Germany. With installed power of well over 200 gigawatts, China is by far the world's largest wind market.
END