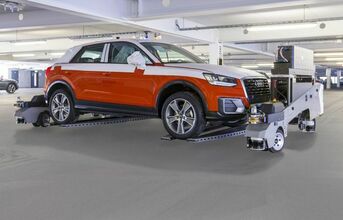
There are now twelve parking robots in use at Audi's main plant in Ingolstadt. They autonomously transport Audi models after production for railway loading. For this, one of the roughly six meter long and three meter wide robots uses laser sensors to determine the position and dimensions of a car and adjusts itself accordingly. Then the robot carefully lifts the car up to ten centimeters.
A central, autonomous control system assigns a space to the robot where the robot can park it via the shortest route. Once a sufficient number of cars have accumulated for the same transport destination, a robot prepares them for loading on to the railway freight cars.
The driverless transport systems complete up to 8,000 movements per day this way, while covering about 500 kilometers (310.7 miles). They even change their own batteries: When the charge status is low, the robots promptly dock themselves onto the automated changing station and specially designed robots change out the batteries within a few minutes.
The system operates reliably around the clock - on an open parking deck and at outdoor temperatures up to minus 20 degrees Celsius (minus 4 degrees Fahrenheit). It thus improves both efficiency and ergonomics for employees: They now have significantly shorter distances to walk and are exposed to fewer extreme weather conditions.
The Ray driverless transport system was created in partnership with Serva Transport Systems in Grabenstätt am Chiemsee. The parking robots are continuously being developed further - their weather resistance, for example. In the first quarter of 2017, a total of 18 parking robots are already sorting ready-to-transport cars in Audi railway loading within an area of 20,000 square meters (215,278.2 sq ft). Additional opportunities for their use in the Ingolstadt plant have already been identified.
END